GB/T36701-2018
埋地钢质管道管体缺陷修复指南
Guidelinefordefectrepairofburiedsteelpipelines
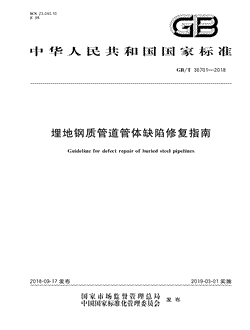
- 中国标准分类号(CCS)E98
- 国际标准分类号(ICS)23.040.10
- 实施日期2019-03-01
- 文件格式PDF
- 文本页数29页
- 文件大小2.63M
以图片形式预览埋地钢质管道管体缺陷修复指南
埋地钢质管道管体缺陷修复指南
国家标准 GB/T36701一2018 埋地钢质管道管体缺陷修复指南 Guidelinefordefeetrepairofburielsteelpipelines 2018-09-17发布 2019-03-01实施 国家市场监督管理总局 发布 币国国家标准化管理委员会国家标准
GB/T36701一2018 目 次 前言 范围 2 规范性引用文件 3 术语和定义 -般规定 数据收集 6 常见的修复方法 典型缺陷的修复 健康、安全、环境 13 质量验收和后期工作 附录A(规范性附录 管道在役焊接作业 14 18 附录B资料性附录数据采集表 附录c(规范性附录复合材料补强修复要求 19 附录D(资料性附录)埋地钢质管道典型缺陷的修复流程 21
GB/36701一2018 前 言 本标准按照GB/T1.1一2009给出的规则起草
本标准由全国锅炉压力容器标准化技术委员会(SAC/TC262)提出并归口
本标准起草单位:特种设备检测研究院、石油化工股份有限公司天然气分公司、石油 天然气股份有限公司长庆油田分公司第一输油处、石化销售有限公司华南分公司、深圳市燃气集团 股份有限公司、中石油管道有限责任公司西部分公司、石化销售有限公司华东分公司、中特检管道 工程(北京)有限公司、石油天然气股份有限公司管道分公司管道科技研究中心、石油化工股份 有限公司华北油气分公司、石油天然气股份有限公司长庆油田分公司第三输油处、惠州市大亚湾华 德石化有限公司、广东省天然气管网有限公司大庆油田有限责任公司天然气分公司、上海金艺检测技 术有限公司、石化管道储运有限公司,陕西省天然气股份有限公司 本标准主要起草人;刘长征、陈杉吉建立、何仁祥,宗照峰、赵宏涛、杨大慎、杨光张晓松、李荐乐、 张华、蔡景明,王富祥、张登宇,那珊珊、李旭光、王立祷、姜绪彪、谢成、谭春波、周吉祥、丁建成,何磊 孙伟.畅卫涛
GB/36701一2018 埋地钢质管道管体缺陷修复指南 范围 本标准规定了埋地钢质管道管体缺陷修复的方法和实施程序
本标准适用于I485/X70及以下钢级的埋地钢质长输管道、集输管道管体缺陷的修复,L485/X70 及以下钢级的其他埋地钢质管道可参照本标准执行
规范性引用文件 下列文件对于本文件的应用是必不可少的
凡是注日期的引用文件,仅注日期的版本适用于本文 件
凡是不注日期的引用文件,其最新版本(包括所有的修改单)适用于本文件
GB/T8923.1一2011涂覆涂料前钢材表面处理表面清洁度的目视评定第1部分:未涂覆过 的钢材表面和全面清除原有涂层后的钢材表面的锈蚀等级和处理等级 GB/T23257 埋地钢质管道聚乙烯防腐层 GB/T28055钢质管道带压封堵技术规范 GB/T30582基于风险的埋地管道外损伤检验与评价 GB/T31032一2014钢质管道焊接及验收 GB50251输气管道工程设计规范 GB50253输油管道工程设计规范 GB50369油气长输管道工程施工及验收规范 NB/T47013.2承压设备无损检测第2部分:射线检测 NB/T47013.3承压设备无损检测第3部分:超声检测 NB/T47013.4承压设备无损检测第4部分;磁粉检测 承压设备无损检测第5部分渗透检测 NB/T47013.5 SY/T4l09石油天然气钢质管道无损检测 sY/T5918埋地钢质管道外防腐层保温层修复技术规范 sY/T6444石油工程建设施工安全规程 术语和定义 下列术语和定义适用于本文件
3.1 修复压力rpair pressure 实施修复时缺陷处管道的操作压力
3.2 永久修复peranentrepair 保证管道在全寿命周期内可靠运行而进行的修复
3.3 临时修复temporaryrepair 保证管道在一定时间内可靠运行而进行的修复,适当时将被永久修复替换
GB/T36701一2018 3.4 凹陷dent 管壁受外部挤压或碰撞产生径向位移而形成的局部塌陷,是由于管壁永久塑性变形而使管道横截 面发生的形状改变
3.5 沟槽guge 因机械作用导致的金属损失,在管壁造成局部的细长沟渠或凹痕
3.6 屈曲buckle 因管道弯曲或轴向压缩荷载造成的管壁全部或部分失稳起皱
3.7 褶皱wrinkle 管道弯头内侧表面的横向不规则纹路
3.8 补板修复patehrepair 通过在管体焊接钢质加强板的方式对缺陷或泄漏进行修复的方法
3.9 A型套筒typeAsleeve 由覆盖在管道缺陷处的一对半圆形钢质护板,经纵向对接焊缝焊接组合而成 注A型套筒无需焊接在管道上,为非承压套筒,可以为缺陷区域提供补强性能,但对管道轴向应力无影响
3.10 B型套筒typeBsleeve 由覆盖在管道缺陷处的一对半圆形钢质护板,经纵向对接焊缝焊接组合而成,套筒末端以环向角焊 的方式固定在管道上
注,B型套筒为承压套筒,可以承受管道内压,也能承受因管道受到侧向载荷而产生的轴向应力
3.11 钢质环氧套筒steelsleevefillelwithepoxyresin 由覆盖在管道缺陷处的一对直径比管道略大的半圆形钢质护板,经焊接或螺栓连接在一起,套筒末 端用密封胶密封,套筒与管道之间的环隙内注人环氧树脂而形成的复合套简
注环氧树脂与套筒之间形成连续的负载过渡,可以将管道承受的载荷均匀地传递到钢质套筒上
3.12 复合材料补强ceopositematerialreinforcement 利用复合材料的高强度和高弹性模量,通过涂敷在缺陷处的高强度填料,以及管体和纤维补强层间 的树脂,将管道承受的载荷均匀地传递到复合材料修复层上
3.13 机械夹具mechamiealclamp 安装在缺陷或泄漏处外部形成密封空腔,提供强度和刚度保证的金属构件
3.14 带压开孔hot-tapping 在管道处于承压或在役状态下,以机械切削的方式去除管体缺陷,加工出圆形孔的作业方式
-般规定 4.1从事管道本体缺陷修复(以下简称“缺陷修复”)的施工单位应具备相应的能力;从事缺陷修复的人
GB/36701一2018 员应具有工艺、材料、焊接、检验、工程等知识和实践经验
4.2缺陷修复所用材料应具有产品合格证等相关质量证明文件,有许可要求的材料,应由取得相应许 可的生产单位制造
4.3管道使用单位应依据检测和适用性评价结果制定修复计划
按照风险高低安排修复顺序,高风险 的缺陷应优先修复
采用临时修复方法修复后,应及时采用永久修复方法替换
4.4缺陷修复步骤一般包括数据收集、方案制定,实施修复、质量验收和后期工作等内容
4.5一种缺陷可能存在多种适用的修复方法,应结合缺陷数据、客观条件和企业运行需求,选择最合适 的修复方法
4.6管道修复涉及焊接作业时,应执行煤接工艺规程,并满足附录A的相关要求
数据收集 5 5.1管道修复位置确定后,宜采取降压措施,并进行开挖,收集与缺陷及修复相关的数据
5.2需收集的数据宜包括以下几个方面 缺陷数据缺陷类型、缺陷尺寸,缺陷位置、缺陷评价结果等; a 管道数据规格(外径、壁厚),钢管类别(无缝钢管、焊接钢管、复合管)材料等级(钢级/材料 b 牌号防腐层类型、安装时间等; 运行数据:介质类型、介质成分、工艺参数(介质流速、操作温度、操作压力等)等 d 环境数据;天气状况、人口密度、环境敏感性、,交通便利性等
5.3数据采集表参照附录B. 常见的修复方法 6.1打磨 6.1.1打磨修复适用于焊接缺陷(电阻焊除外)浅裂纹、电弧烧伤、沟槽等非泄漏缺陷,不适用于修复 凹陷、深裂纹和电阻焊焊缝上的缺陷
6.1.2打磨修复前,应对缺陷区域进行彻底清理,并测量缺陷的纵向长度和剩余壁厚
6.1.3如果打磨深度不超过管道公称壁厚的10%,则打磨长度不受限制;如果打磨深度超过管道公称 壁厚的10%,若满足以下两个条件之一,则打磨深度的最大值可以达到管道公称壁厚的40% 打磨长度不超过按式(1)计算的纵向可接受长度 a =1nG" 式中: 打磨区域的纵向可接受长度,单位为毫米(nm mm; D 管道外径,单位为毫米(mm); 打磨区域的最大测量深度,单位为毫米(mm); -管道公称壁厚,单位为毫米(mm). 管道的最大操作压力(MOP)不大于按GB/T30582计算的管道失效压力与设计系数的乘 b 积,即 MoP
GB/36701一2018 套筒的材料等级一般与待修复管道的材料等级相同,具体材料可根据实际情况确定 c d)套筒的在役焊接应满足附录A的相关要求
6.4.1.3若套筒覆盖区域的管道上有焊缝,宜采取以下措施加强套筒安装的紧密度 通过打磨消除焊缝余高; a b 采用预制了突起或凹槽的凸式套筒或凹槽式套筒
A型套筒 a D B型套筒 说明 -套筒 -管道管体; -纵向对接焊缝; -环向角焊缝
图1套筒示意图 A型套筒 6.4.2 6.4.2.1A型套筒适用于管体金属损失、电弧烧伤、管体或直焊缝上的凹陷、裂纹等缺陷的修复,不适用 于修复环向缺陷、泄漏和会继续发展的缺陷
A型套筒与管壁之间可能存在间隙,有腐蚀和阴极保护失效的风险,宜采取适当的措施密封套 6.4.2.2 筒两端并确保套筒与管道之间的电连续性
6.4.2.3若缺陷长度小于L.,则套简厚度应不小于待修复管道公称壁厚的2/3;若缺陷长度大于或等于 L,则套简厚度应不小于待修复管道的公称壁厚
L按式(3)计算 (3 L=20D 式中 D 管道外径,单位为毫米(mm); 管道公称壁厚,单位为毫米(mm) 6.4.2.4宜采取以下措施提高A型套筒修复的有效性 修复时降低管道操作压力; a b 通过预热套简或对套简施加机械外力的方法,使套简紧贴管壁; 在缺陷处和套筒与管道之间的环隙内填充环氧树脂、聚酯化合物等可硬化材料
c 6.4.3B型套筒 6.4.3.1B型套筒适用于多种类型缺陷的修复,包括泄漏和环向缺陷
6.4.3.2套筒的厚度应不小于待修复管道的公称壁厚
6.4.3.3B型套筒的设计,安装应满足以下要求
GB/T36701一2018 套筒末端角焊缝和管道原有环焊缝的距离不小于管道外径,且不小于150mm:; a b 相邻套简的角焊缝距离不小于管道外径的1/2,若两个套筒的角焊缝距离小于管道外径的 1/2,则不能将套筒相邻端与管体焊接,而应使用另一个稍大的套筒连接这两个套筒 套简与管壁之间的间隙不超过2.5" mm; c d 若套筒修复长度大于管道外径的4倍,修复时应对管道采取临时支撑措施,并分层回填,避免 冲击管道; 修复泄漏缺陷时,应预先封堵泄漏处再安装套筒,可采用堵漏夹具、在套筒上安装引流管等 方式; f 套筒的纵向对接焊缝应采用全熔透焊接技术,其他在役焊接应符合附录A的相关规定
6.5钢质环氧套筒 钢质环氧套简适用于腐蚀.沟槽,裂纹、凹陷、焊接缺陷(环焊缝除外),褶皱、屈曲等非泄漏缺陷 6.5.1 的修复
钢质环氧套筒示意图见图2
6.5.2钢质环氧套筒应具备以下功能结构 定位孔在钢质环氧套简两侧,通过调节定位螺栓的高度而使钢质护板与管道圆周方向的间隙 a 保持一致的螺纹孔; 排气孔;在钢质环氧套简正上方,可排除锅质护板与管道之间的空气以及环氧填料中的气泡 b 并可以指示环氧填料是否滥注完成的孔洞
钢质环氧套筒的设计、安装应满足以下要求 6.5.3 环氧填料在管道运行温度范围内不发生劣化 a 钢质护板的厚度和材料等级应使其具有不低于待修复管道设计压力的承压能力 b 钢质护板长度不小于150mm 且钢质护板末端距离缺陷外侧边界不小于50mm; c 安装时,管体温度高于露点3C且不高于60C,环境相对湿度不高于85%; d 钢质护板与管道圆周方向的间隙保持一致; e 环氧填料和端面密封胶应按产品说明书提供的工艺条件进行配制,并在其有效工作时间内使 f) 用完毕
6.5.4环氧填料固化后,应采用肖氏硬度计测量填料的固化硬度,固化硬度应不小于90Hs 说明: -端面密封胶; -环氧填料; 排气孔; 定位孔 填料注人孔
图2钢质环氧套筒示意图
GB/36701一2018 6.6复合材料补强 6.6.1复合材料补强适用于腐蚀、电弧烧伤、裂纹、沟槽、管体或直焊缝上的凹陷等非泄漏缺陷的修复, 不适用于修复环向缺陷,深度大于80%公称壁厚的缺陷和会继续发展的内腐蚀缺陷
6.6.2复合材料补强修复技术中的复合材料主要是指纤维增强复合材料,包括高强度填料,绝缘层和 纤维补强层(碳纤维、玻璃纤维、凯夫拉纤维等);无论纤维补强层是否导电,均宜在管道与纤维补强层之 间设置绝缘层,以避免发生电偶腐蚀
6.6.3复合材料补强的设计、材料、施工,现场检验和防腐等要求见附录c 6.6.4典型的纤维补强层分别具有以下特性: 碳纤维的弹性模量与钢接近,有利于修复层与钢质管道之间的协同变形,使应力均匀分布,修 a 复补强效果良好;但碳纤维具有导电性,修复时应采取绝缘措施 b 玻聘纤维价格低廉,但其弹性模量比钢小约一个数量级,修复时只有当钢质管道发生较大塑 性变形后,才能将载荷传递到修复层,且抗老化性较差 凯夫拉纤维具有密度低,强度高,韧性好,耐高温、良好的电绝缘性等特点,适用于不规则管件 的缺陷修复
6.7 机械夹具 6.7.1机械夹具主要包括螺栓紧固夹具和堵漏夹具两种
螺栓紧固夹具适用于除褶皱或屈曲外大多 数缺陷的修复,堵漏夹具仅适用于泄漏的修复
6.7.2螺栓紧固夹具通常采用弹性密封,用来承受泄漏的压力;需要使用较大的螺栓来提供足够的夹 紧力
采用螺栓紧固夹具修复时,应同时满足以下要求 螺栓紧固夹具末端距离缺陷外侧边界不小于50mm a b)螺栓紧固夹具的承压能力不低于待修复管道的设计压力; 采用焊接固定时,螺栓紧固夹具的在役焊接应满足附录A的相关要求
c 堵漏夹具主要用于临时修复腐蚀穿孔引起的泄漏
采用堵漏夹具修复时,应同时满足以下 6.7.3 要求 修复压力不高于管道操作压力的80%; a b)工程分析结果显示泄漏周围的腐蚀不会出现裂纹
6.8带压开孔 6.8.1带压开孔适用于局部机械损伤、外腐蚀、沟槽,电弧烧伤、裂纹等缺陷及泄漏的修复
6.8.2采用带压开孔的方法修复在役管道上的缺陷,应按GB/T28055的相关要求实施,并同时满足以 下要求: 缺陷的位置、方向、几何尺寸等数据已准确测量并记录 a 开孔机的尺寸符合缺陷范围需求,即带压开孔切割下来的鞍形板包含整个缺陷 b 开孔管件的在役焊接应满足附录A的相关要求; c d 带压开孔工艺应严格设计,规范施工,以确保管道能够承受开孔过程中产生的各种应力
mm30 6.8.3应预制外径比开孔孔径小15" nmm的鞍形板,并随塞堵安装回管道 6.9换管 6.9.1换管适用于所有缺陷类型及泄漏的修复
6.9.2换管修复可选择采用停输换管或不停输换管
不停输换管一般是通过带压封堵的方式实现,带 压封堵作业应按GB/T28055的要求实施
GB/T36701一2018 6.9.3替换管段的承压能力应不低于待修复管道的设计压力,并预先进行水压试验,试验压力值、稳压 时间及合格标准应符合GB50369的相关要求
6.9.4替换管段的长度应不小于L
L,按式(4)计算 150,D<168mmm 2D,l68mmm D一610mm L 1220,D>610mm 式中 D 管道外径,单位为毫米(mm); L -替换管段的最小长度,单位为毫米(mm)
6.9.5换管修复施工时应满足以下要求 不停输换管或作业环境有可燃气体时应采用机械方法断管 a b 断管后,应对管内和管口进行清理,并采用气囊、黄油墙等隔离措胞 为防止隔离管段内压力积聚,应在隔离管段上开排气孔,并在修复过程中持续检查
c 替换管段与待修复管道应采用对接环焊缝焊接工艺,对于磁偏吹现象严重的管线,应采取消磁 6.9.6 措施,且应按NB/T47013.2或NB/T47013.3,sY/T4109的要求对焊缝进行射线检测或超声检测
典型缺陷的修复 7.1 般要求 7.1.1管道使用单位应依据适用性评价和风险评估结果制定详细的修复计划
修复计划一般包括立 即修复、限期修复和监控使用
7.1.2符合以下条件的缺陷,宜立即修复 金属损失的深度超过管道公称壁厚的80%; a 含应力集中的凹陷(凹陷处存在导致应力集中的其他缺陷) b 缺陷处管道失效压力小于或等于设计压力的1.1倍 e d 应力腐蚀开裂或焊缝选择性腐蚀
7.1.3符合以下条件的缺陷,宜限期修复 凹陷位于管道顶部2/3区域,且深度超过管道外径的6% a 凹陷位于焊缝上,且深度超过管道外径的2% b 缺陷处管道失效压力小于或等于设计压力的1.25倍; c 金属损失的深度超过管道公称壁厚的50%; d 沟槽类缺陷的深度超过管道公称壁厚的12.5%; e 未立即修复的裂纹或潜在裂纹 f 7.1.4符合以下条件的缺陷,宜监控使用 凹陷深度超过管道外径的6%,但位于管道底部1/3区域 a b 凹陷位于管道顶部2/3区域,但深度不超过管道外径的6%
7.1.5修复方法的选择取决于需要修复的缺陷类型,不同类型的缺陷对修复方法有相应的限制,典型 缺陷的修复方法选择概况见表 7.1.6缺陷修复前,宜采取降压措施,修复压力不应超过适用性评价确定的安全工作压力;涉及在役焊 接作业时,修复压力不应超过按附录A计算的允许带压施焊压力
7.1.7换管适用于所有缺陷类型和泄漏的修复,本章所讨论的修复方法不包括换管
GB/36701?2018 1????? ????? A B ? ? ? ?????о?о ? й? ? ? 2a)??(d<0.8) ? ? 2b)??(d 0.8t 2e)??? ? ? " ad)??? ?? ? ? 4a)?? ? 4b)躸???? ? ? 4e)ú? " " 4d)绡 ? ? ? ? ? 6a)?(d<0.4n) ? ? s 6b)(d>0,4t) ?" ? 7a )???? ' ?? 7b )??? 7e)???е ?" " ?? 7d)??е? " ?? ? ? ? 塢 s , ?:d ?,λ?(mm);t -???,λ?(mm). ???????С??? ??о??????? ???Χ?,?С0.!?? ?????,?С0.8?? ??,??????顣 ????????,?С0.l?? ??? ?????С ??ú???????15% ??????? ??????
GB/T36701一2018 7.2腐蚀修复 7.2.1在修复腐蚀缺陷前,应对管道的外腐蚀区域进行彻底清理,以准确测定外腐蚀区域的尺寸,包括 纵向长度和最大腐蚀深度(见图3)
7.2.2若腐蚀不位于凹陷内,且腐蚀区域的尺寸(包括外腐蚀、内腐蚀)满足以下两个条件之一,则无需 进行修复 最大腐蚀深度小于或等于管道公称壁厚的10%或设计壁厚的腐蚀裕量 a b 当最大腐蚀深度大于管道公称壁厚的10%且小于或等于40%时,纵向长度不超过按式(1)计 算的纵向可接受长度或管道的最大操作压力满足式(2)
纵向长度 最大腐蚀深度 图3腐蚀区域测量示意图 7.2.3对于焊缝选择性腐蚀,应采用B型套简、钢质环氧套筒或螺栓紧固夹具的方法进行修复;对于环 向的,环焊缝上的或焊缝热影响区内的腐蚀,应按照环焊缝缺陷(见7.3.3)进行修复
7.2.4对于外腐蚀,若最大腐蚀深度d小于或等于管道公称壁厚的80%,可采用堆煤、补板、A型套 筒、B型套筒、钢质环氧套筒、复合材料补强、螺栓紧固夹具或带压开孔的方法进行修复;若最大腐蚀深 度大于管道公称壁厚的80%,则应采用补板,B型套筒、螺栓紧固夹具或带压开孔的方法进行修复
具 体的修复流程参见附录D图D.1
7.2.5对于内腐蚀,若腐蚀程度不会继续发展超出其临界值,可采用A型套简,B型套筒、钢质环氧套 筒,复合材料补强或螺栓紧固夹具进行修复;若腐蚀可能继续发展,以上方法中的A型套筒和复合材料 补强和螺栓紧固火具则仅作为临时修复措施,应监控使用
具体的修复流程参见图D2. 7.2.6对于点蚀,若点蚀深度大于管道公称壁厚的80%,可采用补板,B型套筒、螺栓紧固夹具的方法 进行修复
采用补板和B型套筒修复时,应采取降压措施
7.3焊接缺陷修复 7.3.1对于直焊缝或螺旋焊缝上的体积缺陷和平面缺陷,可采用打磨、A型套筒、B型套筒,钢质环氧套 筒、复合材料补强、螺栓紧固夹具或带压开孔的方法进行修复
7.3.2对于电阻焊焊缝上或附近的缺陷,可采用B型套简、钢质环氧套筒或螺栓紧固夹具的方法进行 修复
7.3.3在修复环焊缝缺陷前,应采用无损检测的方法对缺陷进行检测
具体的修复流程参见图D.3
要求如下: a 若缺陷为深度不超过公称壁厚10%的表面金属损失且焊缝内部无缺陷,可采用打磨或打磨后 堆焊的方法进行修复; 10
GB/36701一2018 b 若缺陷为深度超过公称壁厚10%的表面金属损失或内部缺陷(气孔,夹渣、未焊透等),则应采 用B型套筒或螺栓紧固夹具进行修复; 若环向缺陷长度大于管道周长的1/12或存在较高的纵向应力,应优先采用B型套筒进行 修复
7.3.4对于电弧烧伤,宜先对缺陷进行打磨,若打磨后异常金相组织已完全消除,则可单独采用打磨或 继续采用堆焊或复合材料补强的方法进行修复;若打磨后异常金相组织没有完全消除,则应继续采用A 型套筒、B型套筒、钢质环氧套筒、螺栓紧固夹具或带压开孔的方法进行修复
7.3.5若采用套简修复焊接缺陷,应采用预制了突起或凹槽的凸式套简或凹槽式套简,以加强套简安 装的紧密度
7.4裂纹修复 7.4.1在修复裂纹前,应采用无损检测的方法对裂纹进行检测,具体的修复流程参见图D4
对于最大深度小于或等于管道公称壁厚40%的浅裂纹,可采用打磨,堆焊,补板、A型套筒,B型 7.4.2 套筒、钢质环氧套筒、复合材料补强、螺栓紧固夹具或带压开孔的方法进行修复
若采用堆焊、补板、A 型套筒、锅质环氧套筒或复合材料补强的方法进行修复,应保证修复前裂纹已通过打磨完全消除
对于最大深度大于管道公称壁厚40%的深裂纹,可采用堆焊、A型套筒、B型套简,钢质环氧套 7.4.3 简、螺栓紧固夹具,复合材料补强或带压开孔的方法进行修复
以上方法中,若采用除带压开孔以外的 其他方法进行修复,应保证修复前裂纹已通过打磨完全消除或修复后的裂纹长度始终小于裂纹扩展临 界值
7.4.4环向裂纹不宜采用A型套筒、钢质环氧套简和复合材料修复技术进行修复
7.5凹陷修复 7.5.1在修复凹陷前,应对凹陷尺寸进行测量,并采用无损检测的方法对凹陷处可能存在的其他缺陷 进行检测
若同时满足以下条件,则无需进行修复 凹陷为普通平滑凹陷(凹陷处不存在导致应力集中的其他缺陷); aa 管体上的凹陷深度小于管道外径(OD)的6%,焊缝上的凹陷深度小于管道外径的2% b) 凹陷长度与深度的比值(L/d)不小于20; c 凹陷处的腐蚀深度不大于管道公称壁厚的10%
d 7.5.2若凹陷影响到清管,则应采用换管的方法进行修复
7.5.3对于普通平滑凹陷,若凹陷位于管体或直焊缝上,可采用A型套筒、,B型套简,钢质环氧套筒、复 合材料补强或螺栓紧固夹具的方法进行修复;若凹陷位于环焊缝上,以上方法中的A型套简和复合材 料补强则不适用
7.5.4对于含应力集中的凹陷,若凹陷位于管体或直焊缝上,可采用打磨、A型套筒、B型套筒、钢质环 氧套筒、复合材料补强、螺栓紧固夹具或带压开孔的方法进行修复;若凹陷位于环焊缝上,以上方法中的 A型套筒、复合材料补强和带压开孔则不适用
具体的修复流程参见图D.5
7.5.5采用A型套筒、,钢质环氧套筒或复合材料补强修复凹陷时,应同时满足以下要求: 凹陷深度不大于管道外径的15% aa 已通过打磨消除了凹陷处的其他应力集中缺陷 b 已使用合适的填充材料填补了凹陷
7.6鼓泡和氢致开裂修复 7.6.1对于鼓泡和氢致开裂,若管道无泄漏,可采用A型套筒,B型套筒、钢质环氧套筒或螺栓紧固夹 具的方法进行修复;若管道已发生泄漏,则只能用B型套筒的方法进行修复
1
GB/T36701一2018 7.6.2若使用B型套简进行修复,应采用超声检测对鼓泡和裂纹进行定位,以避免在鼓泡和裂纹上进 行焊接
7.7褶皱或屈曲修复 7.7.1对于褶皱或屈曲,若通过无损检测的方法确认不存在导致应力集中的其他缺陷,且测量的皱 高度满足式(5),则无需进行修复
褶皱高度测量示意图见图4 7.7.2若褶皱或屈曲影响到清管,则应采用换管的方法进行修复
7.7.3褶皱或屈曲可采用B型套筒或钢质环氧套筒的方法进行修复,套筒的设计应与管道缺陷形状、 尺寸相符
具体的修复流程参见图D.6
外壁 内壁 图4褶皱高度测量示意图 12,S138MPa" 207-S)/69十l,l38MPa324MPa 式中 褶皱高度,单位为毫米(mm); D 管道外径.-单位为毫米(mm) 最大环向应力,单位为兆帕(MPa)
8 健康、安全、环境 8.1 -般要求 管体缺陷修复作业应遵循国家和行业有关健瞧、安全与环境的法律,法规及相关规定
作业前应进 行风险识别、评价,制定风险削减措施和必要的应急预案
8.2安全防护 管体缺陷修复作业的全过程,应有可靠的安全防护措施 开工前,施工单位应组织施工人员进行安全教育,确保所有施工人员充分理解并严格遵守安全 a 操作规程,严格按照经审批的施工方案进行施工组织 b 施工人员应按规定正确使用防护服、安全帽、防护眼镜、手套、工作鞋等劳动防护用品 施工现场应根据消防要求配置消防设施和消防器具,并保持消防通道畅通 c d 开挖作业坑时,应根据土质情况决定边坡坡度,必要时,应采取防塌方措施; 施工现场应设置明显的安全警示标志,作业坑边应设置临边防护; e 12
GB/36701一2018 fD 施工期间应避免管输介质出现剧烈的压力波动,严禁施工期间进行清管、,内涂或内检测作业 有条件的应停输或降压运行; 施工现场环境有影响施工人员健康的粉尘,噪声、有害气体时,应采取有效的防护措施 g h)现场动火作业前应进行可燃气体检测,动火全过程应有专人监护 其他未提及内容按sY/T6444的相关要求执行
8.3环境保护 应清理和妥善处理施工过程产生的废弃物,包括清除的旧防腐层、泄漏的管道介质等;对施工造成 的土地、植被等原始地貌、地表破坏,应按设计要求予以恢复 质量验收和后期工作 9.1质量验收 管体缺陷修复工程的施工质量验收应满足以下要求: a 参与施工质量验收的各方人员应具备相应的资格 b 施工质显应符合本标准及相关专业验收标准的规定,以及设计文件的要求 随工质量的脸收应在施工单位自行检查评定合格的基础上进行 c d 隐蔽工程应在隐蔽前已由施工单位通知有关单位进行了验收,形成验收文件 验收检验项目的抽检结果应符合本标准的相关要求,其检验结果应得到验收组成员共同确认
9.2后期工作 修复作业完成并进行了现场检验后,应按以下要求开展后期工作 由方案中的指定人员告知管道调度运行单位,管道已处于可投人运行状态; a 管道重新启动或恢复压力后,应对修复管段进行现场监控以防泄漏,直至管道恢复正常运行; b 应仔细做好防腐、回填工作,确保不损坏原有或新换管道防腐层,且不产生应力集中 c 在永久修复完成后,应恢复现场地貌,并在地面上埋设标志桩 d 编制竣工资料,应包括但不局限于以下内容缺陷类型、修复方法、所用材料、焊接记录、无损检 测记录、防腐施工记录以及缺陷开挖验证材料等
13
GB/T36701一2018 附 录 A 规范性附录) 管道在役焊接作业 范围 A.1 本附录适用于采用手工电弧焊对在役埋地钢质管道的管体缺陷进行的维抢修焊接作业,包括堆煤 修复、补板修复、套筒修复、换管修复和带压开孔修复
A.2焊接工艺及评定 管道在役焊接前,应根据管道材料、运行参数以及焊接材料等信息制定预焊接工艺规程,按照 GB/T310322014附录D的相关要求进行焊接工艺评定,并依据评定合格的焊接工艺编制焊接工艺 规程
A.3人员要求 A.3.1从事管道在役焊接的焊工和无损检测人员应持有相关部门颁发的资格证书
A.3.2管道在役焊接前,焊工应通过焊工上岗考试,上岗考试应符合GB/T31032一2014的相关要求
焊条的保管和运输 A.4 A.4.1焊条的保管和运输应符合生产厂家的规定,应避免损坏,受潮
包装开启后,应保护焊条不变 质,有损坏或变质迹象的焊条不应使用
A.4.2低氢焊条应妥善保管和使用,以确保其低氢水平
低氢焊条应进行烘干处理,焊条从烘箱中取 出后,应立即进行焊接,1h内未使用完的焊条要放回烘箱继续烘干
A.5在役焊接前的准备工作 A.5.1管道在役焊接前,应对焊接区域进行彻底清理直至漏出金属光泽,必要时,还应通过打磨以满足 焊接要求
A.5.2应使用超声波测厚仪测量焊接位置的管道剩余壁厚,管道在役焊接位置的最小剩余壁厚应不小 于3.2 mm ,且输气管道在役焊接位置的最小剩余壁厚应不小于4.8 mm
A.5.3管道在役焊接时,管道允许带压施焊的压力应满足式(A.1)的要求 2a.(t (A.1 式中 -管道运行带压施焊的压力,单位为兆帕(MPa); -管材的最小屈服极限,单位为兆帕(MPa); o 焊接处管道实际壁厚,单位为毫米(mm); -因焊接引起的壁厚修正量,单位为毫米(mm),按表A.1取值; 14
GB/36701一2018 D 管道外径,单位为毫米mm) F -安全系数,按表A.2取值
表A.1修正量 单位为毫米 媒条直径 2.0 2.5 3,2 4.0 1.4 1.6 2.0 2.8 表A.2安全系数 1/mm 12.7 8,7<12.7 6.4<1<8.7 6.4 0.72 0.68 0,55 0,4 A.5.4应调节介质流速,管道内液体流速应不大于5m/s,气体流速应不大于10m/s
A.5.5缺陷修复工件的装配与组对应满足以下要求 套简、补板或对开三通与管道之间的间隙不应太大,宜使用机械外力,使其紧贴管壁,必要时可 a 在管道上焊接预堆层以减小间隙; b 对焊接缺陷修复工件部位的管道螺旋焊缝和直焊缝宜打磨至母材高度; 对开三通法兰沿管道轴线方向的两端到管顶的距离差应小于1mm,对开三通法兰轴线与其 所在位置管道饷线间距应不大于1.5mm. A.5.6在役焊接的作业环境应满足以下要求 环境温度应不低于5C,相对湿度应不高于90%,在雨雪、风沙等天气条件下,应采取有效的 防护措施后再施焊; b 应利用开挖、搭建平台等手段为焊接创造足够的作业空间 应对可能存在的可燃气体进行浓度检测,可燃气体浓度应低于其爆炸下限的10%
A.5.7管道在役焊接前,应采用火焰加热或中频加热的方式进行预热,预热不仅可以减缓焊接冷却速 度,还能促进氢,水分及其他污染物的扩散挥发
预热应满足以下要求: 预热温度应符合焊接工艺规程的要求,建议预热温度为100C150C; a 管道内部介质温度较低或流速过快时,预热应采用火焰加热和中频加热相结合的形式 b 在整个焊接过程中,层间温度的最小值应不低于预热温度的最小值 c d 当煤接作业中断时,再次焊接前应重新加热到要求的预热温度
A.6在役焊接 A.6.1管道在役焊接应执行焊接工艺规程,焊工应取得相应的焊接资质并通过上岗考试 A.6.2焊接套简或对开三通时,应先同时焊接两侧纵向对接焊缝,再焊接环向角焊缝,且两道环向角焊 缝不应同时焊接;对于其他类型的工件,应采用把残余应力减至最小的焊接顺序
A.6.3纵向对接焊缝的焊接应满足以下要求: 焊接套简或对开三通的纵向对接焊缝时,宜在对接焊缝下装配低碳钢垫板,以防止煤接到管道 上,垫板长度应与套筒或对开三通的护板长度相同或略长,宽度为对接焊缝宽度的2倍 3倍 b 套简或对开三通的纵向对接焊缝应100%焊透,根部间隙对接面的间隙)宜为3mm6mm; 焊道应主要位于套筒或对开三通的护板上,位于垫板上的焊道不应超过2mm宽,否则易烧穿 15
GB/T36701一2018 垫板 d 套简或对开三通的护板长度大于750mm时,每道纵向对接焊缝应由至少2名焊工同时施; 由1名焊工焊接每道纵向对接焊缝时,应按图A.la)所示焊接顺序同时施焊;由2名焊工焊接 e 每道纵向对接焊缝时,应按图A.lb)所示焊接顺序同时施焊
工A 工B 工A 纵向对接焊缝(右) 纵向对接焊缝(右 纵向对接娜缝(左) 纵向对接娜缝(左 焊工B 工C 工D a 2名爆工同时爆接 b 4名焊工同时焊接 图A.1纵向对接焊缝焊接顺序 A.6.4环向角焊缝的焊接应满足以下要求 B型套简或对开三通的护板与管道的环向角焊缝宜采用多道堆焊,一般的堆焊形式见图A.2; a 套筒或对开通护板 说明;数字代表焊接顺序
图A.2环向角焊缝堆焊焊接形式示意图 b)第一条焊道与B型套筒或对开三通的护板距离应小于2mm,但不应与护板连接; 在管道外径大于或等于325mm的管道上进行B型套简或对开三通的环向角炽缝的煤接时 c 每道焊缝应由至少2名焊工同时施焊,且两电弧间应至少相距50mm,焊接顺序见图A.3; B2 D1 B1 D2 2名爆工同时爆接 a 4名焊工同时焊接 b 图A.3环向角悍缝悍接顺序 d)B型套简或对开三通的护板厚度小于或等于管壁厚度的1.4倍时,角焊缝的焊脚高度和宽度 16
GB/36701一2018 应等于护板厚度,见图A.4a); B型套简或对开三通的护板厚度大于管壁厚度的1.4倍时,应把B型套简或对开三通护板的 外表面磨成坡度为1:1的斜面,且角焊缝的焊脚高度和宽度应等于管壁厚度的1.4倍,以减 少应力集中,见图A.4b). 14 套简或对开三通护板 套简或对开兰迎护板 护板厚度大于管壁厚度的1.4倍 b 护板厚度小于或等于管壁厚度的1,4倍 说明 护板厚度; 管壁厚度
图A.4环向角焊缝焊脚尺寸 A.6.5坡口和每层焊道上的锈皮及焊渣,在下一步焊接前应清除干净
在役焊接控制 A.7 A.7.1管道在役焊接主要存在烧穿和氢致开裂两个风险,应综合考虑管道操作压力、流动状态和焊接 处剩余壁厚等影响焊接安全可靠性的因素,采取适当的控制措施
取 A.7.2为防止烧穿,在役焊接应 采 下控制措施: 当管道剩余壁厚小于6.4mm时,打底焊应使用直径不大于2.5mm的焊条 a b 当管道剩余壁厚大于或等 于6.4mm时,打底焊应使用直径不大于3.2mm的焊条
A.7.3为防止氢致开裂,在役焊接应采取以下控制措施 使用低氢焊条或低氢焊接工艺方法; aa b 采用足够的热输人量,规定最小热输人量要求等级,但应防止烧穿; 采用合理的焊接顺序,宜采用回火焊道焊接工艺,多组施焊时,焊接顺序应对称布置; c d 合理装配缺陷修复工件,以减少焊缝根部的应力集中 按A.5.7的要求进行预热,并在焊接后维持加热15min,厚壁管宜适当延长加热时间
A.8焊接质量检验 A.8.1焊接质量的检验、缺陷的清除和返修应按GB/T31032一2014的相关规定执行
A.8.2与管道相连的焊缝易产生焊道下裂纹或延迟裂纹,应按NB/T47013.3、NB/T47013.4或 NB/T47013.5的要求对焊缝进行渗透检测、磁粉检测超声检测或两种检测方法的组合
A.8.3若套筒或对开三通的护板较厚,其纵向对接焊缝和环向角焊缝采用磁粉检测时,宜采用分层检 测的方式 17
GB/T36701一2018 录 附 B 资料性附录) 数据采集表 数据采集表见表B.1
表B.1数据采集表 管道名称 缺陷编号 距上游标志桩(m): 距下游标志桩m) 距上游环焊缝(m) 距下游环焊缝m). 缺陷定位 坐标点:经度 纬度 时钟方位: 口内腐蚀 口外腐蚀 口裂纹 口焊缝选择性腐蚀 口电弧烧伤 缺陷 口环焊缝缺陷 口硬点 口沟槽 口管体焊缝缺陷 缺陷类型 数据 口鼓泡 口氢致开裂 口含应力集中的凹陷 口普通平滑凹陷 口褶皱 口屈曲 口其他 是否泄漏 口是 口否 缺陷尺寸 长mm): 宽(mm): 深(mm): 剩余壁厚( mm 所在部位 口钢管 口三通 口弯头/管 口其他( 管道规格 管道外径(mm) 公称壁厚(mm): 材料等级 钢级: 材料牌号: 口无缝钢管 口直缝埋弧媒管 口螺旋缝埋狐焊管 口高频电阻煤管 俐管类别 口复合管 口其他 管道 口单层熔结环氧粉末 口双层熔结环氧粉末 口环氧煤沥青 数据 口液态环氧树脂 口煤焦油带沥青焦油 口石油沥肯 防腐层类型 口收缩带/套 口泡沫夹克防腐层 口三层PE 口聚乙烯胶粘带 口其他 年 安装时间 管道安装时间: 口成品油 口其他 介质类型 口原油 口天然气 运行 介质成分 数据 介质流速 操作温度(C) 操作压力(MPa): 工艺参数 最大操作压力(MPa): 天气 天气状况 温度(C): 湿度: 风力 环境 是否属于高后果区 口是 口否 后果严重程度 数据 是否属于环境敏感区 口是 口否 交通便利 大型施工机械是否可达 口是 口否 年 采集人 年 月 日 审核人 18
GB/36701一2018 录 附 C 规范性附录 复合材料补强修复要求 设计要求 C.1 根据缺陷评估结果和管道运行情况,制定复合材料补强修复方案,修复层的设计应满足以下要求: 修复层与缺陷处管道剩余壁厚之和的承压能力应不小于待修复管道的设计压力 a b 复合材料的使用温度范围应包含待修复管道的运行温度范围; 复合材料的性能应不受管道输送介质的影响 c d 专用树脂的玻璃化转变温度应比待修复管道的运行温度高15C以上
C.2 材料要求 C.2.1复合材料应符合设计要求,使用前宜对关键技术指标进行性能抽检复验
C.2.2复合材料应具有产品说明书、合格证、性能检验报告、安全数据表等技术资料;复合材料的存储、 运输和详细的设计,安装要求应符合制造商的相关规定
C.2.3复合材料应在保质期内使用,若纤维布放置时间超过2个月,使用前应在烘箱内用60C干燥 2h后方可继续使用
C.3 施工要求 c.3.1补强修复的施工过程应遵守制造商和管道使用单位的相关规定,作业人员应经过充分培训
c.3.2现场开挖应以缺陷点位置为中心,开挖尺寸、放坡要求、土壤堆放等应按照sY/T5918的相关规 定执行
c.3.3补强修复前,应清除管道表面防腐层,管体表面处理应满足以下要求 清除原有防腐层的长度应至少超出缺陷外侧边界各500mm,清除后的管道表面应无明显的 涂层残留,清除过程中应避免损伤管体金属; b)待修复区域管道表面的除锈等级应达到GB/T8923.1一2011中规定的Sa2.5级或St3级,并 应采用干燥的空气吹扫或清洁刷除去表面的粉尘和残留物 管道表面除锈后.补强修复应在4h内进行,若超出规定时间,应重新进行表面除锈
c C.3.4修复施工的环境条件应符合复合材料产品说明书的规定
若无明确规定,应满足以下要求: 管体温度应高于露点3C且不高于60 C,环境相对湿度应不高于85%; a 施工环境应无粉尘,在雨雪、风沙等天气条件下,应采取有效的防护措施后再进行施工
b C3.5高强度填料和专用树脂应按产品说明书提供的工艺条件进行配制,并搅拌均匀;加人固化剂后, 应在有效的工作时间内使用完毕 C3.6采用湿缠绕法修复施工时,纤维布缠绕应满足以下要求 应根据设计确定的修复层轴向总长度,以缺陷处为中心进行缠绕,使纤维与管道轴向垂直 a b 修复层末端距离缺陷外侧边界应不小于100mm,且修复焊接缺陷时应不小于400mm:; 若缺陷之间轴向距离小于25mm或环向距离小于管道公称壁厚的6倍,则视为同一缺陷区 域,可进行连续缠绕修复; 19
GB/T36701一2018 d 纤维布轴向搭接长度应为纤维布幅宽的20%一40%,周向搭接长度应不小于200 mm 环向缠绕纤维布长度不足时,继续缠绕纤维布搭接长度应不小于200mm; e D 修复螺旋焊管上的缺陷时,纤维布缠绕方向应与管道螺旋焊缝走向相反 复合材料层间应无气泡,纤维布应被树脂完全浸润; 8 h 修复弯头时,应采用适当宽度的纤维布以避免褶皱,弯头内侧纤维布轴向搭接长度应为纤维 布幅宽的75%~80%,外侧搭接长度应不小于纤维布幅宽的50%.
C.3.7采用预成型法修复施工时,预成型复合材料的粘贴应满足以下要求 安装起始垫时,应确保管体缺陷位于预成型复合材料中间位置,距离缺陷外侧边界应不小于 a 100mm; b 预成型复合材料的起始端应紧贴起始垫,并与管道轴向垂直; c 胶黏剂应涂抹均匀,预成型复合材料层间、预成型复合材料与管壁之间应无空隙
C.3.8修复层固化期间,应使用遮挡物防止沙尘、雨水等污染修复层表面
若环境温度低于15C,可 采取加热措施加快固化加热温度应不高于60C
C.3.9修复层固化后,宜对修复区域进行定位标记,便于以后内检测定位
现场检验要求 修复层固化后,应对施工质量进行现场检验修复层应满足以下要求 检查修复层的外观和几何尺寸,修复层实际的轴向长度应不小于设计要求,位置偏差应不大于 a) 0mm,纤维布褶皱高度应不大于2.5mm,树脂颜色应均匀一致; 采用涂层测厚仪测量圆周方向均匀分布的4点的修复层厚度,结果应符合设计要求; b 用小锤轻敲修复层表面了解空鼓情况,缺陷位置附近100mm内应没有空鼓,整体空鼓率应不 超过5%; 采用巴氏硬度计测量修复层的固化硬度,固化硬度应不小于40HBa; d 每20处修复点至少抽1处按照GB/T23257规定的方法测定修复层的剥离强度,不足20处 e 时至少抽1处,剥离强度应不低于70N/em
C.5防腐要求 现场检验完成后,应对修复区域进行防腐处理,防腐层施工过程控制和质量验收应符合sY/T5918 的规定
新防腐层与原防腐层的搭接宽度应不小于100mm 20
GB/36701?2018 ?D ?? ?????? D.1???????D.1 ?? d/>0.8 ??? 7.2.2) 1. ·? 2. 3.A? 4.B? ?й? 5.?? 6.??? 7??о 1,B? 1.B? 8.? 2.??о 2.? 3,? 3.?о(? ·? · ·? ?D.1?????? 21
GB/T36701?2018 D.2???????D.2 ?? ? й 1.B? ? 2.?о(? l.B? ·? 2.??о ?? ·? ? 1.A?(? 1.A? 2.B? 2.B? 3.???(? ? 3?? 4.??о(? (7.2.2) 4??? 5??о ·? ·? ·? ?? ?? ?D.2?????? 22
GB/36701一2018 D.3环焊缝缺陷的修复流程见图D.3
环郎缝缺陷 是否发生 泄漏 娜缝内部是否 有缺陷 表面金属损失 深度>0.I7 1.打磨 2.堆娜 环向缺陷长度管道 B型套筒 用长的服存在较 3.B型套筒 高的纵向应力 4螺栓紧固夹具 重新防腐和回填 1.B型套筒 重新防腐和回填 2.螺栓紧固夹具 重新防腐和回填 图D.3环焊缝缺陷的修复流程图 23
GB/T36701?2018 D.4????D.4 ? йл 1.B? 2.??о ?λ? ???? 3.? ·? 1.B? ?? 2,?? ? 3.??о 1.B? ??绡 ·? 2.??о 3? ?? ·? ?? ·? 1.A? 2.B? 3?? 4.??о 5.? ·? ?D.4??? 24
GB/36701?2018 D.5????D.5 ?? ?? ?? е? ?λ 6%OD ? l.? 1.? ?λ 2.A? 2.B? ? 3.B? 3.?? 4.?? 4.??о 5.??? 6,??м 2%OD 7.? ·? ?<0.1n /d/20 ·? ?λ ? 1.A? 2.B? 1.B? 3.?? 2.?? 4.??? 3??о .??о ·? ·? ?D.5??? 25
GB/T36701一2018 D.6褶皱或屈曲的修复流程见图D.6
褶皱或屈曲 是否影响 清管 换管 帮皱高度是否 可接必 1.B型套简 燃皱处是否存在 尊数应力中的 2.钢质环氧套简 其他缺陷 重新防腐和回填 里新防腐和回填 图D.6褶皱或屈曲的修复流程图 26