GB/T25383-2010
风力发电机组风轮叶片
Windturbinegeneratorsystem-Rotorblades
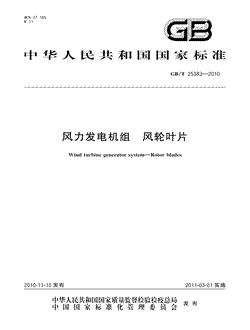
- 中国标准分类号(CCS)F11
- 国际标准分类号(ICS)27.180
- 实施日期2011-03-01
- 文件格式PDF
- 文本页数17页
- 文件大小491.41KB
以图片形式预览风力发电机组风轮叶片
风力发电机组风轮叶片
国家标准 GB/T25383一2010 风力发电机组风轮叶片 windturbinegeneratorsystem一Roorbhlades 2010-11-10发布 2011-03-01实施 国家质量监督检验检疫总局 发布 国家标准化管理委员会国家标准
GB/T25383一2010 目 次 前言 范围 规范性引用文件 术语和定义 缩略语 设计环境条件 设计要求 材料要求 制造控制 工艺要求 10检验规则和验收 ll 标识和随机文件 12包装、贮存,运输和吊装 附录A规范性附录叶片结构强度分析方法
GB/T25383一2010 前 言 本标准的编写参考了IEC61400-12005年8月第3版)风力发电机组一第1部分;设计要求 IECTs61400-232001年4月第1版风力发电机组一第23部分:风轮叶片全尺寸试验 IECTR61400-242007年4月第1版)风力发电机组一第24部分;防雷,近海风力发电机组认证规范 德国船级社(2005版)和陆上及近海风力发电机组风轮叶片设计及制造(DNV-OS-J102)2006年版等 标准,对风力发电机组风轮叶片的设计、制造工艺、材料、检验规则以及叶片的包装运输和贮存等有关 内容给出了通用性技术要求,供国内开发研制风力发电机组风轮叶片参照执行
本标准的附录A为规范性附录
本标准由机械工业联合会提出
本标准由全国风力机械标准化技术委员会(SAc/Tc50)归口
本标准主要起草单位;中航惠腾风电设备股份有限公司、上海玻璃钢研究院、连云港中复连众复合 材料集团有限公司,金风科技股份有限公司 本标准主要起草人;田野、田卫国、姜兆民、庄岳兴、赵建立、王逸波、陈余岳、刘卫生、王相明
GB/I25383一2010 风力发电机组风轮叶片 范围 本标准规定了风力发电机组风轮叶片的通用技术条件
本标准适用于风轮扫掠面积等于或大于40m'的水平轴风力发电机组风轮叶片
规范性引用文件 下列文件中的条款通过本标准的引用而成为本标准的条款
凡是注日期的引用文件,其随后所有 的修改单(不包括勘误的内容)或修订版均不适用于本标准,然而,鼓励根据本标准达成协议的各方研究 是否可使用这些文件的最新版本
凡是不注日期的引用文件,其最新版本适用于本标准
GB/T1447纤维增强塑料拉伸性能试验方法(GB/T1447一2005,IsO527-4:1997,NEQ GB/T1448纤维增强塑料压缩性能试验方法 (GB/T1449纤维增强塑料弯曲性能试验方法(GB/T1449一2005,IsO14125;1998,NEQ GB/T1463纤维增强塑料密度和相对密度试验方法GB/T14632005,ASTMD792:1998 NEQ GB/T2576纤维增强塑料树脂不可溶分含量试验方法GB/T2576一2005,IsO308;1994. MOD GB/T2577玻璃纤维增强塑料树脂含量试验方法(GB/T2577一2005,IsO1l172:1996,MOD) GB/T2900.53电工术语风力发电机组(GB/T2900.53一2001,IC60050-415:1999,IDT) GB/T3354定向纤维增强塑料拉伸性能试验方法 GB/T3355纤维增强蛆料纵横剪切试验方法 GB/T3356单向纤维增强塑料弯曲性能试验方法 单向纤维增强塑料平板压缩性能试验方法 GB/T3856 GB/T3961纤维增强塑料术语 质量管理体系要求(GB/T190012008,Iso9001;2008,IDT) GB/T19001 风力发电机组风轮叶片全尺寸结构试验(GB/T25384一2010,IECTs61400-23- GB/T25384 2001,MOD GB/Z25427风力发电机组雷电防护(GB/Z25427一2010,IECTR61400-24-2002,MOD) Iso12944.3涂料和油漆 -用保护涂料进行钢结构防腐第3部分;设计依据 ISO12944.5涂料和油漆 -用保护涂料进行钢结构防腐第5部分;涂料保护系统 IEC61400-1;2005风力发电机组第1部分;设计要求 术语和定义 GB/T2900.53,IEC61400-l;2005和GB/T3961确立的以及下列术语和定义适用于本标准
3.1 设计寿命designlift 在设计工况下的设计使用年限
3.2 风轮 rotor 将风能转化为机械能的风力机部件,由叶片和轮毂组成
GB/T25383一2010 3.3 blade 叶片 使风轮旋转并产生气动力的部件
4 3. referencechord 参考几何弦 指在叶片设计过程中叶片展向某一确定位置处的几何弦,叶片其他位置的几何弦以此位置为参考
-般定义为0"位置,即该处几何弦与风轮旋转平面平行
3.5 扭角twist angle 叶片当地几何弦与叶片参考几何弦的夹角
3.6 中弧线medianlime 翼雅上下表面内切圆圆心光滑连接起来的曲线
在前部,最小内切圆与翼型周线的切点是中呱线 的起点;在后部.最小内切圆与翼型周线的切点是中狐线的终点
3.7 前缘 leadingedge 翼型中弧线的最前点
3.8 后缘 tailingedge 翼型中弧线的最后点
3.9 弦线ehordl 连接前缘与后缘的直线
3.10 弦长chorllength 弦线的长度
3.11 重心 thecentreofgravity 在重力场中.物体处于任何方位时,所有各组成质点重力的合力通过的那一点
缩略语 叶片 风力发电机组风轮叶片 纤维增强塑料 复合材料 设计环境条件 总则 5 1 风力发电机组风轮叶片是一种全天候条件下运行的产品,设计和制造叶片时应考虑环境因素对其 设计寿命的影响
55 温度 2 叶片工作环境温度范围一10C十40C,生存工作温度范围一20C十50C,超出上述规定范 围的,按s级处理
5 湿度 叶片设计工作环境最高相对湿度一般小于或等于95%
GB/T25383一2010 7.1.3材料供应商应提供材料的合格证、材料数据单、检验单、安全数据单和使用说明书
7.1.4主要材料和用于重要零部件的材料进厂后应进行性能复验,试验类型和范围按技术文件和质量 管理体系相关规定进行
7.1.5选用的材料应符合当地相关法律法规的要求
7.2纤维增强塑料 7.2.1树脂 复合材料叶片常用的基体树脂根据其化学性质不同分为环氧树脂、不饱和聚酯树脂,乙烯基 树脂等 7.2.1.2基体树脂在固化状态下有好的防潮性和高的防老化性能,能够满足叶片在不同地点运行所承 受的温度变化、紫外线老化、海水环境腐蚀等要求和足够的抗水解能力
7.2.2增强材料 7.2.2.1复合材料叶片常用的增强材料有玻璃纤维、碳纤维、芳纶纤维和其他有机或无机材料纤维及 其制品
7.2.2.2纤维表面应有浸润剂,纤维表面浸润剂的种类应与基体树脂匹配
夹芯材料 闭孔结构的硬质泡沫塑料可作为夹层板的芯材,应能与所选用的基体树脂和胶粘剂匹配
夹芯材料应具有防老化、防海洋环境腐蚀和工业环境影响的能力及低吸水性
用作芯材的木材应进行防腐和杀虫处理,并进行消毒、均化和烘干,其平均水分含量不大 7.2.3.3 于12%
胶粘剂 纤维增强塑料间或与其他材料间的粘接,应使用无溶剂的胶粘剂,应使用双组分反应型胶粘 剂
如可能,应使用与产品相同性质的树脂
7.2.4.2层合板只能在固化状态下相互粘接
使用热固性胶粘剂时胶粘剂的放热峰值不能超过层合 板的许用温度值
7.2.4.3胶粘剂应具有良好的抗潮湿和抗老化能力
温度对其强度的影响应尽量小,应能在60C以 上的环境温度长期使用
7.2.5预浸料 预浸料应满足制造组件的要求并适于保存
7.2.6外部涂层 外部涂层应具有较好的防紫外线老化性能、抗海洋环境腐蚀,并具有良好的附着力、耐磨性、高弹性 和低吸水性
油漆和胶衣都可用于叶片表面防护的外部涂层
填加的颜料应不受气候的影响,可由无机或光照不褪色的有机染料组成
当使用胶衣时应验证其与基体树脂的匹配性
7.2.7纤维增强塑料层合板试验方法 纤维增强塑料性能的测试方法推荐按下列国家标准进行,测试试件个数至少6件
玻璃纤维增强塑料树脂含量按GB/T2577进行
纤维增强塑料密度按GB/T1463进行
纤维增强塑料纵横剪切性能按GB/T3355进行
单向纤维增强塑料压缩性能按GB/T3856进行
单向纤维增强层板弯曲性能及模量按GB/T3356进行
GB/T25383一2010 纤维增强塑料弯曲性能按GB/T1449进行
纤维增强塑料压缩性能按GB/T1448进行
纤维增强塑料拉伸性能按GB/T1447进行
7.3金属材料 7.3.1应根据具体使用要求选择适当的金属材料
7.3.2应采用适当的方法控制和排除金属材料的制造缺陷;同时,应采用适当的表面处理和热处理工 艺提高金属材料的使用性能和耐环境能力
7.3.3 金属材料性能、化学成分应符合国家标准或其他有关技术条件 制造控制 8.1生产作业文件 生产作业文件依据设计图样和材料特性编制
8.1.1 8.1.2生产作业文件必须明确叶片所有零件的全部制造过程
8.1.3生产作业文件至少应包括材料清单、工具清单,操作要求、检验项目和操作检验记录单等内容 8.2控制内容 8.2.1叶片材料控制 叶片原材料控制按7.1要求进行
8.2.2叶片制造控制 8.2.2.1叶片制造记录文件应跟随生产过程,并纳人叶片档案
8.2.2.2对于影响叶片性能和工艺控制的主要材料,应随叶片制造过程同时制作足够的试样并进行 保存 叶片成品质量检验 8.2. 3 应对部件的加工过程及完成的叶片成品进行检验,特别注意气泡、夹杂、分层,变形、贫胶等
8.2.3
对叶片表面及部件内部缺陷可采用目测、敲击、X射线或超声波等无损检测方法来检验
2 工艺要求 9.1总则 9. 1.1应隔离生产区和储存区,避免层铺材料受到污染
9.1.2在叶片成型过程中,生产区不允许有产生粉尘的加工、,油漆喷涂等作业
9.2成型车间 9.2.1成型车间应满足制造工艺对环境的要求
一般要求环境温度为16C一25C,相对湿度小于或 等于70%,并通过温度计和湿度计进行监测记录
9.2.2成型车间应采取适当措施,防止阳光直射影响树脂正常固化
9 .3 原材料库房 9. .3.1所有原材料应按照其使用说明书的要求进行贮存和取用,并符合国家和地方相关法律,法规 要求
9 .3.2原材料库房内贮存的物品应具有明显的材料标记、贮存条件和贮存周期等标识
9.4成型过程 9 .4.1叶片成型可以采用手糊成型,真空吸注,预浸料或缠绕等方法
9.4 层铺作业应符合有效的技术文件要求,并重点控制铺层的位置、纤维方向和平直状态等
9.4.3应采用适当的方法混合树脂与固化剂,注意尽量少地卷人空气
必要时,可在真空条件下排出 树脂混合物中的空气 树脂浸溃应均匀,充分,复合材料纤维含量应满足设计要求
GB/T25383一2010 9.4.5叶片和零部件应在树脂固化后启模,采用加温固化的叶片和零部件启模后应进行后固化处理
9 4.6待粘接表面应采用适当的方法处理(如打磨,脱脂或底涂等)以保证粘接强度
9 4.7对于被切割的复合材料端面,应采用密封处理,防止外部介质或潮气侵人
9 4.8对叶片制造过程中产生的缺陷可以进行修补,修补后的叶片应满足设计要求
9.5模具 9.5.1模具应保证叶片的外形尺寸公差和稳定性
g.5.2模具的型面和定位尺寸应定期标定以保证叶片外形尺寸的稳定性
9.6工装及计量器具 9.6.1叶片制造所需工装,设备和工具等应满足工艺要求及其他有关规定
9.6.2所用量具,衡器、仪表需经检定,并在检定合格周期内使用
人员要求 9.7 叶片制造人员、检验人员必须经过专门职业培训,经考核合格后可以持证上岗
技术培训时间不得 低于3个月
9.8记录 叶片制造过程中所有零部件、材料以及操作过程应进行连续的和可追溯的记录,这些记录应至少在 两倍的质保期周期内得到保存
检验规则和验收 10 10.1检验分类 10.1.1叶片的检验分型式试验和出厂检验
10.1.2当有下列情况之一时应进行型式试验 新产品试制完成时 -叶片关键材料代用时; 重大工艺调整时 出厂检验与上次型式试验结果有较大差异时; -国家质量监督机构提出进行型式检验要求时等
10.2型式试验 10.2.1叶片型式试验至少应包括: 固有频率测试; 静力试验 疲劳试验 -对于具有叶尖制动机构的定桨距叶片还应进行叶尖制动机构功能试验
10.2.2客户与制造商协商的其他试验项目
10.2.3叶片型式试验方法按GB/T25384《风力发电机组风轮叶片全尺寸结构试验》的规定进行
10.3出厂检验 10.3.1叶片出厂检验至少应进行以下项目: -叶片长度 -叶根接口尺寸; -叶片质量和重心位置; -叶片外观质量目视检查; -叶片内部缺陷应进行敲击或无损检验; -对于具有叶尖制动机构的定桨距叶片应进行功能试验
10.3.2 客户与制造商确定的其他检验项目
GB/T25383一2010 10.4判定规则和复验规则 10.4.1型式试验中只要有一项指标不合格,就应采用另一片新叶片对该项目进行复验,直至合格 为止
10.4.2检验结果与产品图样和技术要求不符时,即为不合格品
10.5不合格品处理 不合格叶片应做明显标记,禁止与合格叶片混放,并应单独存放和处理
标识和随机文件 叶片的标识 叶片的标识包括铭牌,重心标记和叶片零度安装角标记 叶片铭牌应用耐环境材料制作,并固定在叶片根部,包括下列内容 制造商名称.,详细地址 叶片规格,型号 -叶片的长度、重量和重心位置; -叶片系列编号和制造日期; -叶片配套号 -其他项目
11.1.3应在叶片表面标记叶片重心位置
11.1.4应用耐环境材料制作叶片零度安装角标记,并固定在叶片根部
11.2叶片使用维护说明书 11.2.1叶片制造商应提供叶片使用维护说明书 11.2.2叶片使用维护说明书的内容 制造商 名称,型号; -叶片技术数据 -叶片安装原理图 -叶片安装,运输过程中的吊装位置及吊装要求; 叶片贮存要求; -叶片使用维护要求
11.3其他随机文件 叶片制造商应提供用户《叶片接口图样(规范)》、《叶片安装、使用和维护说明书》和《叶片吊装、,运输 和现场存放规范》等文件
包装、贮存、运输和吊装 12 12.1包装 12.1.1叶片复合材料部分表面不需要包装
12.1. 叶根接口部位的螺栓或内孔螺纹应进行有效保护,避免在存放、装卸和运输等过程中损伤或 锈蚀
12.1.3叶片根部应采取有效密封措施,防止尘土或杂物进人叶片内部
12.1.4叶片随机文件 叶片的随机文件应包括下列内容 -装箱单; -随机备件,附件清单;
GB/T25383一2010 叶片合格证; -叶片使用维护说明书; -其他有关的技术资料
12.1.5备件,安装工具和随机文件应装到一个包装箱内,以确保在保管和运输中的完整性
12.2贮存 12.2.1叶片可以露天存放,但要对叶片进行适当保护,避免损坏叶片表面
12.2.2野外存放叶片时,应考虑现场地形和风向的影响,必要时应采取适当的保护措施
12.3运输 12.3.1对于叶片的薄弱部位(如后缘),在运输过程中应进行有效保护如安装适当的保护罩)
12.3.2在运输过程中,每片叶片至少需要两个支撑点,一个支撑在叶根处,另一个在叶片长度约2/3 距叶根)处
支撑叶片主体时,为了均匀承受载荷需要使用与当地翼形基本一致的支撑垫板
12.3.3 叶片运输时,不允许水平放置叶片,即不允许叶片最大弦长处弦线平行于地面 4 12.3 12.3.5建议采用汽车运输叶片
吊装 12.4 吊装叶片时,应采取叶片前缘向下方式
吊点位置后缘应使用后缘防护罩,其长度不小于 500mm. 吊装叶片时,不允许在叶片下面垫硬性支撑物,以免造成结构纤维形成损伤
12.4.2 在吊装过程当中,需要转动叶片时,在叶片后缘应使用后缘防护罩,其长度不小于500mm. 12.4.3 12.4.4对于有叶尖制动系统的叶片,在吊装时,不允许将叶尖和主体之间的连接轴作为吊装点
GB/T25383一2010 附 录A 规范性附录 叶片结构强度分析方法 A.1总则 1)叶片的结构强度分析可参考本附录推荐的方法
(2)叶片结构强度分析主要包括叶片结构动力特性分析、强度分析,变形分析和胶接强度分析
(3叶片强度通常由静强度分析和疲劳分析(设计极限状态校核)来验证
受压部件还应校验失 稳(分层,折皱,翘曲等 (4叶片的主要材料为增强纤维,叶片强度计算主要对增强纤维强度进行校核
(5强度分析应在足够多的截面上进行,被检验的截面的数目取决于叶片类型和尺寸,但至少应 分析四个截面
在几何形状和/或材料不连续的位置处应分析附加的截面
6 用螺纹、胶接或其他连接技术在不同部件间构成的连接强度,应依据设计载荷进行验证
A.2叶片动特性分析 为了避免风力发电机组在运行过程中产生共振,应确定叶片在运行和静止时的一阶挥舞和摆 振方向的固有频率
必要时,还应考虑轮毂和变桨轴承的影响
当叶片长度大于30m时,应对叶片挥舞方向和摆振方向的二阶频率和一阶扭转频率进行 分析 叶片运行时的挥舞和摆振频率应避开机组激振频率的倍频(推荐考虑1P8P),应控制在倍 频士5%以外
叶片结构动力特性分析时应采用叶片材料测试模量的平均值
A.3增强纤维 A.3.1 总则 强度分析既可用应变验证又可用应力验证,对于应力验证,还应分析最大载荷作用点的应变" 证明没有超过破坏极限
验证采用下面A.3.2中叙述的试验数据确定的特征值来进行,应证明设计值s,不超过材料 的许用值R.,(特征值N,除以该材料局部安全系数了 : SR/Y=Ra 如果设有进一步验证,载荷传递区域沿纤维方向的平均应力值应小于10N/mmn 3 如果没有供验证的试验结果,可以使用下面给出的最小特征值
在开始生产前,应能证明材 4 料至少达到在分析中设定的特征值
A.3.2特征值 特征值一般按公式(A.1)计算
1 R,(a,P,,n) A.1) [-(- 式中: U -i%正态分布分位数 试件个数; n 试验值的平均值;
GB/T25383一2010 n个试验值的变异系数
对于公式(A.1),假设观测值的标准偏差符合正态分布,存在的不准确性用缩减系数进行 处理
应采用假设的正态分布中,a=5%、P=95%置信度),此时 1.645 R.(5%.95%,0,n) 一1.645- - A.2 A.3.3材料的局部安全系数 A.3.3.1材料的局部安全系数7M分别定为: 静强度验证(r=a) -疲劳验证(r=b); 稳定性分析(r=c); 胶接分析(r=d和.r=e). 这些系数由局部安全系数Y和缩减系数C相乘而得
YM=YnIIC 对于所有的分析,局部安全系数Y为: 7=1.35 温度影响系数C的适用范围为-30C50C,并且复合层在50C的剪切模量和弯曲模量值比 23C时的值下降不低于20%
下面所列的缩诚系数C
不需更进一步验证,也可以使用试验验证过的缩减系数
A.3.3.2在静强度验证中,>,的值为Y乘以缩减系数C
确定,考虑材料性能的影响,应采用下面的 缩减系数 C
=1.35 老化影响 C 温度影响; 预浸、缠绕方法或树脂注人方法铺敷成型; =1.2 湿法手工铺敷成型 后固化处理, C=1.0 非后固化处理
A.3.3.3在疲劳验证中,应按y乘以下面的缩减系数C确定 C=N”包含载荷循环次数N和s/N曲线斜率m的高周疲劳曲线;朋应通过分析(S/N曲线 确定; 对于玻璃纤维(纤维体积含量:30%
GB/T25383一2010 结构的拉伸强度特征值; R R 结构的压缩强度特征值; S/N曲线斜率; R 结构特征值
当循环次数为1时,R.A=(R.+|R|/2; N 容许载荷循环次数; -材料局部安全系数(按A.3.3.2,静强度); YAMM -材料局部安全系数(按A.3.3.3,疲劳强度); 7w C=N1",见A.3.3.3,7n/Cw,即>中不考虑Cn)
对于给定的作用载荷,可用古德曼图确定容许循环次数N,然后用于损伤累积计算
损伤D定义 为现有载荷循环次数n,与容许循环次数N之比的总和,D小于等于1: D-习<" A.4) 式中: D 损伤; 第i级载荷作用下的循环次数; n 第i级载荷作用下的容许循环次数
N A.4.3纤维间失效分析 对于铺层中的单一层,在相关临界位置,裂纹应按A.4.1第2部分采用计算的方法进行验 证
对于此验证,平行于和垂直于纤维方向的允许失效应力和失效应变以及剪切的允许失效 应力和失效应变是必需的,特征参数应使用缩减系数(>,C)进行缩减,但由(y,C)获 得的系数不应小于1.35
注:横向应变可采用计算或试脸方法确定
如果计算显示出铺层中的单一层不能够传递分配到的应力,则作用在断裂层上的分力4!F 应被其他层分担
根据应传递的分力F的值按表A.1确定
Cw! 不必对有裂纹铺层中单一层因载荷传递引起的应力变化进行精确的描述 纤维内部失效分析中的C取值 表A.1 在纤维内部失效形式中需传递的分力AF 按纤维方向的失效形式 0<4F<5%时的C 4F>5%时的Cm 剪力与横向拉伸的组合 0.6 0.8 剪力为主,与横向压缩的组合 0.6 0.8 横向压缩为主,与剪力的组合 0.8 A.4.4稳定性分析 对拉伸、压缩和/或剪切载荷作用下构件的稳定性(抵抗翘曲和起皱的能力),应在作用载荷的 设计值S的基础上进行验证
对于稳定性分析,为了确定构件强度设计值R,应将材料局部安全系数Y用于材料的刚度 平均值,y应根据局部安全系数y乘以下面的缩减系数C确定 对于整体的铺层和夹芯结构的蒙皮,考虑模量的分散度; =1.3 对于芯材,考虑模量的分散度; =1.0 对于芯材,在使用最小特征值时; 温度影响
-般情况下,当使用计算的方法进行验证,真实结构不能被详细分析时,对其所做的假设和估 计应偏于保守
12
GB/T25383一2010 4稳定性分析可采用(几何)非线性有限元计算方法,对于每个载荷,应采用固有一阶线性屈曲 的无应力预变形
固有一阶线性屈曲的整体比例应按临界起皱的最大高度为其最大水平长 度(弦长)的1/400执行
如果起皱高度已被验证,可允许其有较小的预变形
在上述情况 下,容许应力不应超过已考虑的载荷设计值
在使用非线性有限元法进行稳定性分析时,为了确定屈曲临界载荷,应使用线性有限元法进 行附加验证
屈曲临界载荷必须大于特征载荷值
另外,必须能够证明在预变形出现屈曲 后,邻近的结构构件和结构零件不会出现损伤(如在粘接接合部位). 如果稳定性分析为线性分析时,应考虑附加安全系数1.25
稳定性分析采用试验验证的方法
这种情况下,应考虑载荷设计值和缩减系数,其中取C=1.0. A.5变形分析 1)为了保证叶片与机组其他零部件间的最小间隙,应对所有设计工况下的叶片变形进行验证
当采用静态方式进行叶片变形计算时,叶片在所有运行工况下的最小间隙应不小于叶片在自 2 由状态下与机组其他零部件间隙的40%
叶片在所有静止工况下的最小间隙应不小于叶片 在自由状态下与机组其他零部件间隙的5%
当采用动态或气弹的方式进行叶片变形计算时,叶片在所有运行工况下的最小间隙应不小于 叶片在自由状态下与机组其他零部件间隙的30%
A.6胶接 胶接强度应按A.4通过必要的变换进行分析,应考虑胶接表面和缺陷处的应力集中
1 应遵守制造厂商规定的使用限制,胶接设计应尽最大可能避免剥离力矩或力
2 (3)如果分析是基于试验中得到的特征值,应对每一种情况进行检查,以便于把在试件上发现的 应力集中应用到实际结构构件中去
必要时,特征值应按各种应力集中进行比例修正 为了确定静态的剪应力曲线,应在23C和50C时对使用的胶粘剂进行层间剪切试验或等效 试验
对所确定的特征值应使用材料局部安全系数y
7应由局部安全系数Y和下述 缩减系数C的乘积确定 Cu=1.5 老化影响系数; 温度影响系数 C2a=1.0 Cu=1.1 胶接界面重现性; 后固化处理" Cd=1.0 -1.1 非后固化处理
当不进一步进行验证时,对于双组分的热固性胶粘剂,剪切应力可采用以下特征值 T从=7N/mm 结构中由于应力集中而增大的剪切应力可以使用该值的1.0~3.0倍的数值计算
6 对于疲劳验证,特征s/N曲线应在23C时通过试验确定
对所确定的特征s/N曲线应使 用材料局部安全系数>c
应由局部安全系数>和下述缩减系数C
的乘积确定: C=1. 0 备用系数 温度影响系数; 胶接界面重现性; =1.0 后固化处理; =1.1 非后固化处理
在疲劳验证中应计人平均应力的影响
7)对于双组分的热固性胶粘剂,如果对于循环次数为10”时由当量等幅变程谐得出的应力变程 13
GB/T25383一2010 小于以下值时,应提供在具有连续的剪切应力曲线的连接处(例如大梁和壳体或上下壳体之 间的连接)的疲劳验证
T刚=1.0N/mm 结构中由于应力集中而增大的剪切应力可以使用该值的1.0~3.0倍的数值计算
对于集中载荷的疲劳验证(如金属嵌人物),应在23C时由试验确定特征S/N曲线,应计人 湿度对胶接的影响
应变分析 当叶片结构主要承力材料为单向纤维增强材料时,其静强度和疲劳强度可采用简化的应变分析
沿纤维方向的应变值应低于以下的设计值: 1)玻璃纤维增强材料 拉伸应变 0.35% E8. -0.25% 压缩应变 M/, 碳纤维增强材料 拉伸应变 0.24% ER. 压缩应变 -0.18% EM. 14