GB/T18442.7-2017
固定式真空绝热深冷压力容器第7部分:内容器应变强化技术规定
Staticvacuuminsulatedcryogenicpressurevessels—Part7:Rulesofpressurestrengtheningforinnervessels
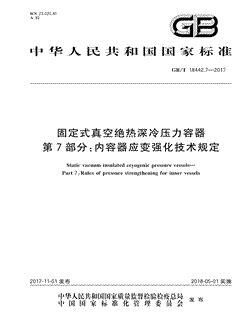
- 中国标准分类号(CCS)A82
- 国际标准分类号(ICS)23.020.40
- 实施日期2018-05-01
- 文件格式PDF
- 文本页数23页
- 文件大小1.63M
以图片形式预览固定式真空绝热深冷压力容器第7部分:内容器应变强化技术规定
固定式真空绝热深冷压力容器第7部分:内容器应变强化技术规定
国家标准 GB/T18442.7一2017 固定式真空绝热深冷压力容器 第7部分:内容器应变强化技术规定 Staticvaeuuminsulatederyogenicpressureyessels- Part7:Rulesofpressurestrengtheningforinnervesses 2017-11-01发布 2018-05-01实施 国家质量监督检验检疫总局 发布 国家标准化管理委员会国家标准
GB;/T18442.7一2017 目 次 前言 范围 2 规范性引用文件 术语和定义及符号 -般要求 材料 设计 制造与检验 应变强化内容器制造过程中重要质量控制点 附录A资料性附录) 附录B资料性附录奥氏体不锈钢钢号近似对照及要求 附录c(资料性附录)应变强化工艺验证性试验要求 12 l6 附录D资料性附录)试件预拉伸及试验规则 附录E(规范性附录)应变强化处理 19
GB;/T18442.7一2017 前 言 GB/T18442《固定式真空绝热深冷压力容器》分为以下7个部分 第1部分:总则; 第2部分;材料 第3部分:设计; 第4部分;制造; 第5部分;检验与试验; 第6部分;安全防护 -第7部分:内容器应变强化技术规定
本部分为GB/T18442的第7部分
本部分按照GB/T1.1一2009给出的规则起草
本部分由全国锅炉压力容器标准化技术委员会(sAcC/Tc262)提出并归口
本部分起草单位;特种设备检测研究院、上海市气体工业协会、浙江大学、华东理工大学、国家 质检总局特种设备安全监察局、查特深冷工程系统(常州)有限公司、张家港中集圣达因低温装备有限公 司、南通中集罐式储运设备制造有限公司、江西制氧机有限公司、荆门宏图特种飞行器制造有限公司,合 肥通用机械研究院
本部分主要起草人陈朝晖、周伟明,郑津洋、寿比南、尹立军、膝俊华,惠虎、徐锋、谢铁军、徐惠新、 王淑华、罗永欣、陈燕山、魏蔚、肖学文、缪存坚、范志超
GB;/T18442.7一2017 固定式真空绝热深冷压力容器 第7部分:内容器应变强化技术规定 范围 GB/T18442的本部分规定了采用应变强化技术建造固定式真空绝热深冷压力容器的内容器(以 下简称内容器)的材料、设计、制造与检验等方面的技术要求
本部分适用于同时满足下列条件的内容器 a 符合GB/T18442.1中1.2的规定,盛装介质为冷冻液化气体; b材料为奥氏体不锈钢; c 名义厚度不小于4mm且不大于24mm,由单一直径的圆简和标准椭圆形封头构成; d)在室温下完成应变强化处理
本部分不适用于盛装毒性危害程度为中度及以上介质的内容器
规范性引用文件 下列文件对于本文件的应用是必不可少的
凡是沫日期的引用文件,仅注日期的版本适用于本文 件
凡是不注日期的引用文件,其最新版本(包括所有的修改单)适用于本文件
GB/T150(所有部分)压力容器 GB/T228.1金属材料拉伸试验第1部分;室温试验方法 GB/T229金属材料夏比摆锤冲击试验方法 GB/T232金属材料弯曲试验方法 GB/T2653焊接接头弯曲试验方法 GB/T3808摆锤式冲击试验机的检验 GB/T12160单轴试验用引伸计的标定 GB/T14976流体输送用不锈钢无缝钢管 GB/T16825.1静力单轴试验机的检验第1部分;拉力和(或)压力试验机测力系统的检验与 校准 GB/T18442.118442.6固定式真空绝热深冷压力容器 GB/T24511承压设备用不锈钢钢板及钢带 NB/T47010承压设备用不锈钢和耐热钢锻件 NB/T47013.2承压设备无损检测第2部分;射线检测 NB/T47013.5承压设备无损检测第5部分:渗透检测 47013.11 承压设备无损检测第11部分;x射线数字成像检测 NB/T47014 承压设备焊接工艺评定 NB/T47016承压设备产品焊接试件的力学性能检验 NB/T47018.1承压设备用焊接材料订货技术条件第1部分:采购通则 NB/T47018.2承压设备用爆接材料订货技术条件第2部分;钢焊条 NB/T47018.3承压设备用焊接材料订货技术条件第3部分;气体保护电弧焊钢焊丝和填充丝 NB/T47018.4承压设备用焊接材料订货技术条件第4部分;埋弧焊钢焊丝和焊剂
GB/T18442.7一2017 JB4732一1995钢制压力容器分析设计标准(2005确认) TSG21一2016固定式压力容器安全技术监察规程 术语和定义及符号 3.1术语和定义 GB/T18442.1界定的以及下列术语和定义适用于本文件
3.1.1 强化压力strengtheningpressure 奥氏体不锈钢制内容器在室温下进行应变强化处理时,容器顶部所达到的最高压力
3.1.2 应变强化容器pressurestrengthenedvessel 奥氏体不锈钢制内容器在室温下施加强化压力进行应变强化处理,卸载后使壳体发生总体塑性变 形并达到结构稳定的容器
3.2符号 下列符号运用于本文件 -断后伸长率,%; 筒体或封头内直径, ,mm; KV 夏比冲击吸收能量,J: LE 侧膨胀值,mms 计算压力,MPa; 强化压力,MPa 抗拉强度,MPa; R 钢材规定残余延伸率为0.2%时的应力,MPa; m.,2 钢材厚度, ,mm [[o,] 内容器应变强化后,筒体或封头材料在设计温度下的许用应力,MPa
般要求 4.1内容器的材料、设计、制造与检验及标识除应符合本标准所有部分的规定外,还需遵守国家颁布的 有关法律、法规、安全技术规范及相关标准的规定
4.2超出本部分范围采用应变强化技术制造内容器时,应按TsG21中的相关规定执行
4.3制造单位应在本单位进行内容器的制造,对其采用的焊接工艺和应变强化工艺进行验证,并对工 艺文件的正确性和完整性负责
4.4制造单位应将产品焊接试件力学性能数据和应变强化试验过程数据及时上传至全国应变强化深 冷容器制造信息公共服务平台
4.5特种设备监督检验机构应对内容器采用的应变强化工艺及参照附录A提出的重要质量控制点进 行监督检验,并满足本部分的要求
GB;/T18442.7一2017 5 材料 5.1钢板 5.1.1钢板的牌号及力学性能应符合表1的规定,供货状态为固溶热处理状态,且满足G;B/T150.2和 GB/T24511的要求
5.1.2钢板应进行复验,至少包括下列内容 逐张检查钢板的表面质量和材料标记 a 按批复验钢板的室温拉伸性能; b) 若采用开平板,其复验要求还应符合GB/T150.4的相关规定
c 5.1.3拉伸试验的取样数量和位置符合GB/T24511和GB/T150.2的规定
5.1.4拉伸试样尺寸和试验方法应符合GB/T228.1的规定
表1钢板力学性能 室温拉伸 号 钢 规定残余延伸率为0.2%时的 抗拉强度 断后伸长率 应力R间e/MPa R/MP A/% S30408 220 520720 49072o S30403 210 >45 S31608 >22o 520~720 S31603 多210 490720 5.1.5当钢板抗拉强度高于720MPa时,应按7.4.1重新进行焊接工艺评定,评定合格后方可采用
5.2钢管与管件 5.2.1俐管与管件用材料应符合GB/T18442.2的规定
5.2.2管件采用冷成形加工时,其成形后的铁素体测量值应不大于15%
5.3锻件 与介质接触的不锈钢锻件应符合GB/T18442.2和NB/T47010的规定,级别不低于I级
5.4焊接材料 5.4.1焊接材料应符合GB/T18442.2和NB/T47018.147018.4的相应规定
5.4.2内容器壳体采用的焊接材料其熔敷金属化学成分应与母材相同或相近,焊接接头强度和韧性与 壳体母材相匹配
5.5境外牌号材料 内容器材料采用境外牌号时,宜参照附录B的规定执行
5.6其他材料 当采用表1和表B.1以外的材料建造应变强化技术制造内容器时,还应符合TSG21的相关规定
GB/T18442.7一2017 6 设计 6.1 -般要求 6.1.1内容器设计除应符合本部分的规定外,还应符合TsG21,GB/T150和GB/T18442.3的规定
6.1.2设计单位应针对应变强化制真空绝热深冷容器出具风险评估报告,其内容除符合GB/T150.1 的规定外,还应包括采用应变强化技术可能产生的失效模式及其风险控制
6.1.3内容器的设计图样中应注明“采用应变强化技术”,以及强化压力,强化前直径等内容
6.1.4本章涉及的内容器直径、厚度等均为应变强化处理前的参数,不考虑应变强化处理后的变化
6.1.5产品铭牌中应标明“应变强化容器”,符号为“Ps” 6.2载荷 6.2.1 内容器设计时,应拨照GB/T18442.3的规定考虑相应的载荷及其组合 6.2.2应变强化处理过程中,还应考虑内容器支撑处产生的支反力和强化压力载荷
6.3许用应力 6.3.1筒体和封头用钢板的许用应力按表2确定
6.3.2接管和锻件等受压元件的许用应力按GB/T150.2确定
6.3.3接管、内容器支承以及开孔部位等局部应力按JB4732校核时,筒体和封头总体薄膜应力的设计 应力强度取值按表2确定,其他受压元件的设计应力强度按GB/T150.2规定的相应材料许用应力 确定
表2应变强化后钢板的许用应力 应变强化许用应力 钢 号 [o,] S30408 273 S31608 S30403 266 S31603 6.4内压计算 内容器的强度计算应符合GB/T150.3的规定,其他相关计算符合GB/T18442.3的规定
6.5外压计算 6.5.1各元件的外压稳定性计算,应符合GB/T150.3的规定,其外压曲线按相应材料20C时选取 6.5.2外压计算压力按下列要求确定,且取大值: a 不小于制造、运输、装卸、检验与试验或者其他工况中,可能出现的最大内外压力差; b)不小于0.04MPa
GB;/T18442.7一2017 6.6开孔补强 内容器的开孔应采用整体补强结构,开孔补强的计算应符合GB/T150.3或JB4732的规定
6.7 强化压力 强化压力,按式(1)进行计算: =1.5户 6.8耐压试验压力 耐压试验压力应符合GB/T18442.3的规定
6.9泄漏试验压力 按照GB/T18442.3的规定进行
6.10结构设计 6.10.1内容器除最后一道封闭环焊缝外,A,B类焊接接头应采用全焊透对接接头,封闭环焊缝允许采 用带永久性垫板的对接接头
6.10.2内容器开孔直径一般不大于1501 nmm
当设置工艺人孔时,开孔边缘应在封头中心0.8D内 开孔中心线沿壳体法线方向
6.10.3加强圈的拼接焊缝应采用全截面焊透焊接接头
加强圈与筒体之间的焊缝应采用双面连续煤 接,州脚高度应不小于筒体厚度和加强圈厚度的较小值
应按额定充满率在内容器上设置溢流口
确定额定充满率时,一般采用应变强化前的内容器 6.10.4 几何容积
6.10.5结构设计时,还应考虑由于内容器塑性变形对容器低温绝热性能,外壳安装及管路系统产生的 影响
制造与检验 7.1 -般要求 7.1.1内容器的制造、检验与验收除应符合本部分规定外,还应满足GB/T18442其他部分和设计文件 的要求
7.1.2制造单位应具备与应变强化工艺相适应的厂房设施、强化装备以及相应的检测设备等
7.1.3制造单位首次采用应变强化技术进行内容器制造前,应试制样品容器,并按TsG21的要求进行 试验验证
强化工艺验证性试验参照附录C的规定
7.2材料制备 7.2.1内容器筒体相邻筒节应优先采用同一炉批号、同一厚度的钢板
采用不同炉批号材料时,相邻 筒节材料的R.,相差不宜超过30MPa
7.2.2内容器封头用钢板宜选择S30403或S31603材料
7.2.3拼接封头应选用同一炉批号的钢板
7.3加工成形 7.3.1内容器的加工应符合GB/T18442.4的相关规定
GB/T18442.7一2017 7.3.2封头如采用S30408奥氏体型不锈钢材料,成形时应采用温成形等适当的工艺对其过渡段和直 边段的马氏体含量进行控制,成形后各部位的铁素体测量值应不大于15%
7.4焊接 7.4.1焊接工艺评定 7.4.1.1内容器施焊前应按照NB/T47014和本部分的要求进行焊接工艺评定
7.4.1.2焊接工艺评定试件的焊接接头外观应无咬边、裂纹、表面气孔,焊渣、凹坑、焊瘤等缺陷,且表面 无焊接飞溅物,试件应按NB/T47013.2进行100%射线检测,技术等级不低于AB级,合格级别不低于 7.5中规定的合格级别
7.4.1.3试件按7.4.1.2的规定经检验合格后,应避开缺陷区域位置制取预拉伸试件,保留焊缝余高,且 参见附录D的规定进行预拉伸处理
7.4.1.4预拉伸后的试件制成试样时,采用机械方法去除焊缝余高,使之与母材齐平
试样取样方法、 规格及加工应分别符合GB/T228.1,GB/T229,GB/T2653和NB/T47014的相应规定
7.4.1.5试验要求: 试样数量 a 取室温拉伸试样2件,弯曲试样4件(2件面弯和2件背弯或生件侧弯),焊缝金属区及热影响 区冲击试样各3件
b 试验温度 拉伸试验和弯曲试验取室温,冲击试验温度不高于内容器最低设计金属温度
试验结果评定 焊接工艺评定试验结果应符合表3的规定,其中焊接接头每组标准试样的冲击吸收能量平均 值应不低于规定值,允许有一个试样的冲击吸收能量低于规定值,且不低于规定值的70%
当试样厚度小于5mm时,其冲击试验仅考核侧膨胀值
表3预拉伸后焊接接头力学性能和弯曲性能合格指标 室温拉伸 抗拉强度 断后伸长率 材料牌号 R./MPa A/% S30408 520 S316o8 25 S30403 490 S31603 冲击试验 夏比冲击服收能量 试样规格 侧膨胀值 材料牌号 KVa/J LE/mm mmm S30408 10×10×55 >31 S30403 7.5×10×55 >24 >0.53 S3l608 5X10X55 l6 S31603 室温弯曲 弯曲试验的弯头直径为4倍试样厚度,弯曲角度180"时拉伸面无裂纹为合格 注;侧膨胀值合格指标均为规定的最小值
GB;/T18442.7一2017 7.4.2焊缝形状尺寸 7.4.2.1焊缝形状尺寸及表面质量除应符合GB/T18442.4的规定外,A类焊接接头焊缝余高还应满 足下列要求 s10mm a 时,焊缝余高不宜大于1mm b 10mm <0,<24mm时,焊缝余高不宜大于0.1d. 7.4.2.2相同厚度的焊接接头,其对口错边量(见图1)应符合下列要求 A类焊缝不大于对口处钢材厚度的15%,且不大于2" a mm b B类焊缝不大于对口处钢材厚度的15%,且不大于3 mm
图1A,B类焊接接头对口错边量 7.4.3强化前焊缝返修 强化前焊缝返修应符合GB/T18442.4的规定
7.4.4强化后焊缝焊接返修和施焊 7.4.4.1当筒体A,B类焊接接头和公称直径大于50mm的接管与筒体的D类焊接接头焊接返修后, 应重新进行应变强化处理,并经制造单位技术负责人批准
7.4.4.2当符合下列情况施焊时,可免除再次应变强化处理,但应进行耐压试验,试验压力按6.8确定 仅承受较小载荷附件的点煤; aa 接管的焊缝长度不超过内容器内直径的10%,且不超过100 b mm; 对主体结构不产生显著影响的轻微的焊缝返修
c 7.4.5产品焊接试件 7.4.5.1应逐台制备产品焊接试件,试件应在简节纵向焊缝的延长部位与筒节同时施焊
强化前几何 容积小于或等于5m的内容器纵向焊缝,采用相同的焊接工艺时,允许以批代台制备产品焊接试件
同型号,同批次、同材料牌号、同焊接工艺和同强化工艺的内容器可以组批,每批不超过20台
7.4.5.2产品焊接试件宜按附录D的规定进行预拉伸
产品焊接试件和试样数量应符合NB/T47016 的规定
预拉伸后的室温拉伸,室温弯曲与低温冲击(不高于最低设计金属温度)试验及其合格指标应 符合表3的规定
7.5无损检测 7.5.1应变强化实施前检测 内容器所有A、B类焊接接头应按NB/T47013.2或NB/T47013.11进行100%射线检测,检 a 测技术等级不低于AB级,除带垫板的封闭焊接接头合格级别不低于级外,其余焊接接头的 合格级别不低于I级;
GB/T18442.7一2017 b 内容器A,B,DE类焊接接头及加强圈与内容器的角接焊接接头等应力集中的部位应按 NB/T47013.5进行100%渗透检测,合格级别不低于I级 起弧点和临时附件切除后的焊接处应修磨至圆滑过渡并按NB/T47013.5进行渗透检测,合 格级别不低于I级; d 经检测发现不允许的缺陷时,应对超标缺陷进行返修,并对该部位按原检测要求和合格级别 进行重新检测和评定
7.5.2应变强化过程的检测 当压力升至设计压力时,对内容器表面进行目测检查,应无泄漏,无可见变形,无异常响声为 a 合格; b 强化后压力卸压至设计压力时,应对内容器的焊接接头进行形状尺寸检查、外观目视检查,应 无渗漏、无异常声响为合格
7.5.3应变强化实施后检测 带垫板的封闭焊接接头应按NB/T47013.2或NB/T47013.l1进行5%射线检测,检测技术等 a 级不低于AB级,合格级别不低于目级,检测部位优先选择丁字焊缝和原有条形缺陷部位 T形焊缝和7.5.1中b).o)要求的焊缝,应按NB/T47013.5进行100%渗透检测,合格级别 b 对 不低于I级; 经检测发现不允许的缺陷时,应在缺陷两端的延伸部位均增加不少于250mm的补充检测,如 仍有不允许的缺陷,则对该条焊缝进行100%检测
对超标缺陷应进行返修,并对该部位按原 检测要求和合格级别进行重新检测和评定; 符合7.4.4.2规定的施焊部位,应按NB/T47013.5进行100%渗透检测,合格级别不低于 d 级
7.6应变强化处理 内容器应变强化处理应符合经验证合格的强化工艺文件和附录E的规定
7.7耐压试验 当内容器强化后焊缝的炽接返修和施焊符合7.4.4.2的规定时,应按本部分和其他部分的要求进行 耐压试验
GB;/T18442.7一2017 录 附 A 资料性附录 应变强化内容器制造过程中重要质量控制点 A.1设计文件 A.1.1风险评估报告
A.1.2文件的完整性和标准符合性
A.1.3设计文件中的“Ps”标识
A.2材料复验 A.2.1内容器材料应满足第5章的要求
A
.2.2筒体和封头的材料还应符合7.2的规定
成形控制 A.3.1筒体和封头的成形应符合7.3的规定
A.3.2焊缝形状尺寸应符合7.4.2的规定
A.4焊接工艺评定 焊接工艺评定应符合7.4.1的规定,预拉伸后焊接接头的力学性能和弯曲性能合格指标应符合表3 的规定 A.5焊接 A.5.1应按评定合格的焊接工艺进行施焊
A.5.2焊材的选择应符合5.4的规定
A.6产品焊接试件 产品岸接试件应符合了.45的规定,其力学性能和弯曲性能合格指标应符合表了的规定 无损检测 A.7 A.7.1内容器应在强化实施前,强化实施过程中及强化实施后进行无损检测
A.7.2检测方法、检测比例及合格指标等应符合7.5的规定
A.7.3应注意强化前有缺陷的部位和应力集中部位在强化后的检测结果
GB;/T18442.7一2017 附录 B 资料性附录 奥氏体不锈钢钢号近似对照及要求 B.1本附录给出了相应境外牌号材料与本标准所采用材料的对应关系,见表B.1
B.2当表B.1中的境外牌号的材料用于采用应变强化技术制造内容器时,其化学成分和力学性能等应 符合第5章的相关要求
表B.1奥氏体型不锈钢钢号近似对照表 ASME(2013 GB/T245112009 EN10028-7;2007 SA240 号 牌 号 牌 统一数字代号 数字代号 UNS代号 型号 S30408 06Crl9Nil0 l.4301 X5CrNil8-10 S30400 304 S30403 022Cr19Ni10 l.4306 X2CrNil9-l1 S30403 304l S31608 06Crl7Ni12Mo2 X5CrNiMol7-12-2 s31600 l.4401 316 S31603 022Crl7Ni12Mo2 1.4404 X2CrNiMo17-12-2 S31603 316L 11
GB/T18442.7一2017 附 录 C 资料性附录) 应变强化工艺验证性试验要求 C.1一般要求 C.1.1内容器制造前其工艺文件应经工艺验证性试验进行验证
验证试验采用试制样品容器,并参见 附录D的要求进行相关试验
C.1.2样品容器的设计、制造和检验应符合本部分的要求,并在试制前根据本部分及相关标准的要求 进行焊接工艺评定,制定焊接工艺指导书、应变强化工艺指导书和试验大纲等工艺文件
C.1.3验证试验的相关要求应按照试验大纲的内容和要求进行
样品容器的结构要求 样品容器的结构要求如下 C.2.1 罐体至少为2个筒节,每筒节宽度不小于1500mm,对接环向焊缝设置在预估内容器变形最大处 a 内直径不小于1800mm,名义壁厚不小于8mm b c 罐体不设加强圈、人孔、支座垫板等约束性部件 d 筒体与封头的对接环向焊缝应能模拟内容器封闭焊缝的焊接接头形式
C.2.2按样品容器的结构和设计参数进行强度计算
C.2.3样品容器应变强化工艺可进行数值仿真,通过与试验结果对比,掌握采用应变强化工艺造成筒 体的塑性变形的部位及变形量的规律
C.3验证性试验大纲 c.3.1 -般要求 验证性试验大纲应明确在应变强化实施前、强化过程中和强化实施后的检验和试验项目、目的、方 法和要求
C.3.2验证性试验项目、实施时机和试验目的 见表C.1
试验项目、实施时机和试验目的 表C.1 序号 试验项目 试验阶段 试验目的 本试验是检测样品容器的焊接接头内外部相关缺陷和母材表面 强化前 缺陷以发现超标缺陷和线状表面缺陷 媒接接头无损检测 本试验是检测样品容器的焊接接头内部缺陷和母材表面缺陷,以 强化后 发现新的超标缺陷和线状表面缺陷的扩展情况 12
GB;/T18442.7一2017 表C.1续) 序号 试验项目 试验阶段 试验目的 强化前 金相组织分析 本试验是检测样品容器母材和焊接接头的金相组织、晶粒度和夹 选择项 渣等,并对比分析其奥氏体和马氏体组织变化情况 强化后 马氏体含量测试 用铁素体含量测试仪对强化实施前的封头过渡段、直边段部位的 强化前 选择项 马氏体含量进行测试 强化前 设计压力时 筒体周长测量的目的是按应变强化工艺要求测量样品容器筒体 强化压力时 周长变化情况,并计算周长变化率,为强化结束提供判据
简体周长测量 保压过程 样品容器再次加压到计算压力时周长的测量是为了了解样品容 卸压后 器筒体的弹性变形情况 计算压力时 再次卸压后 A、B类焊接接头 本试验是检测样品容器强化后A、B焊接接头的力学性能,以验 强化后 力学性能检验 证其性能是否符合本部分要求 本试验是检测取样品容器强化前母材的力学性能,以验证其性能 母材力学性能检验 强化前 是否符合本部分要求 产品焊接试件 本试验是检测取样品容器产品焊接试件强化后的力学性能,以验 预拉伸后 力学性能检验 证其性能是否符合本部分要求 C.3.3试验内容 C.3.3.1焊接接头无损检测 焊接接头的无损检测应符合7.5的相关规定 C.3.3.2马氏体含量测试 用铁素体含量测试仪对强化前的封头过渡段、直边段的马氏体含量进行测试
C.3.3.3筒体周长长度测量 C.3.3.3.1强化实施前测量 在内容器开始强化前对筒体进行周长测量,周长测量位置选在各拘束段预估可能产生最大变形的 截面部位
强化实施过程中及强化实施后测量 C.3.3.3.2 在强化过程中及强化实施后测量,应对预估可能产生最大变形的截面进行周长测量
13
GB/T18442.7一2017 C3.3.4强化后力学性能检验 C.3.3.4.1取样原则 应避开超标缺陷处取样 C.3.3.4.2取样位置、测试项目及合格指标 取样位置、测试项目及合格指标如下 取样位置见图C.1,要求如下 a 筒体周向最大变形截面处的纵向焊缝试件; 1 2 筒体周向最大变形截面处的临近环向焊缝试件 33 封头拼接焊缝试件; 筒体与封头连接处带垫板环向焊缝试件 4 简体与封头连接处不带垫板环向焊缝试件; 5 6 产品焊接试件,应满足7.4.5的要求,并按附录D的规定进行预拉伸
A向 90 周向最大变形截面处 180 3# 225 270 说明: -筒体周向最大变形截面处纵向焊缝试件 -筒体与封头连接处带垫板环向焊缝试件; 1井 筒体周向最大变形截面处的临近环向媒缝试件;5# -筒体与封头连接处不带垫板环向媒缝试件 2井 3井 -封头拼接炽缝试件 图c.1样品容器取样示意图 b 测试项目及合格指标见表C.2
表C.2测试项目及合格指标 样品容器取样位置 测试项目 要 合格指标 求 取样后需要把弧面展平 拉伸(常温1个) 拉伸试样轴向垂直于媒缝" 21 冲击(一196C低温6个,州 3 冲击试样长度方向垂直于炽缝,V形缺 样品容器焊接 缝和热影响区各3个) 口的轴线平行于板厚方向垂直于 表3 接头试件 弯曲常温2个,面弯十背弯 表面); 1个 各 弯曲试样轴向垂直于媒缝媒缝中心应 对准弯心轴线 14
GB;/T18442.7一2017 表C.2(续) 样品容器取样位置 测试项目 要 求 合格指标 拉伸(常温1个) 拉伸试样轴向垂直于焊缝" 1 冲击(一196C低温6个,焊 2 冲击试样长度方向垂直于焊缝,V形缺 产晶焊接试件 表3 缝和热影响区各3个) 口的轴线平行于板厚方向 预拉伸后 弯曲试样轴向垂直于焊缝,焊缝中心应 3 弯曲常温2个,面弯十背弯 各1个 对准弯心轴线 原始母材简体) 拉伸(常温1个) 拉伸试样垂直于板材轧制方向 表1 的力学性能试件 15
GB/T18442.7一2017 附 录 D 资料性附录) 试件预拉伸及试验规则 D.1 试验设备 D.1.1拉伸试验机采用计算机控制,测力系统按GB/T16825.1校准,精确度不低于1级,数据采集和 处理按GB/T228.1中附录A的规定
D.1.2引伸计应符合GB/T12160的规定,精确度不低于1级
D.1.3夏比摆锤冲击试验机应符合GB/T3808的规定
D.2焊接试件预拉伸 D.2.1焊接试件预拉伸试样 预拉伸试样尺寸为原始钢板全厚度(T)×宽度(W)×长度(L)
带焊缝的试样应保留焊缝余高,焊缝应 位于试样中间部位
预拉伸试样的有效区域应为远离上下夹头20mm的范围内
预拉伸试样见图D1
图D.1预拉伸试样 D.2.2焊接试件预拉伸方法 D.2.2.1焊接试件预拉伸方法可采用应力控制法或应变控制法
D.2.2.2采用应力控制法时,应满足如下要求; a 预拉伸时,应保证预拉伸试样与试验机的同轴度; b 平均应力加载速率不大于1MPa/s:; 达到预拉伸终止应力值后,保持载荷不变进行保载,保载时间不少于15min后卸载,应变率不 c 大于0.1%h
预拉伸终止应力值见表D.l; 焊接试件性能试验报告中,应有预拉伸加载的应力-时间以及位移-时间的关系曲线图
表D.1焊接试件预拉伸终止应力值 号 钢 预拉伸终止应力值/MPa S30408 410 S31608 30403 00 S31603 16
GB;/T18442.7一2017 D.2.2.3采用应变控制法时,应满足如下要求 a 预拉伸前,根据试验条件确定标距尺寸,以试件中心为基准向两侧进行标距划线,标距尺寸应 300 在200mm" mm之间 b 预拉伸时,应保证预拉伸试样与试验机的同轴度 c 平均应力加载速率不大于1MPa/s; d)以标定的标距,进行9%的总应变控制,达到9%应变后卸载
D.3室温拉伸试样和试验方法 D.3.1室温拉伸试样 D.3.1.1拉伸试样尺寸 室温拉伸试样为比例试样,并符合GB/T228.1的规定
D.3.1.2试样制备 室温拉伸试样的制备应符合GB/T228.的规定
带焊缝的室温拉伸试样,应去除焊缝余高,焊缝 应位于试样平行段的中间部位,试样的厚度应等于或接近试样母材的厚度
焊缝两侧母材厚度不一致 时,试样厚度应与较薄侧一致
D.3.2室温拉伸方法 室温拉伸试验按GB/T228.1的要求进行
D.4冲击试样和试验方法 D.4.1冲击试样 D.4.1.1制取尺寸为10nmm×10mm×55mm的夏比V型缺口冲击试样,也可按试件的厚度制取尺 寸为7.5mm×10mm×55mm或5mm×10mm×55mm的夏比V型缺口冲击试样,冲击试样应符 合GB/T229的规定
D.4.1.2每个冲击试样的V型缺口均需在专用的缺口投影仪进行测量,合格后方可进行试验
D.4.2冲击试验方法 冲击试验方法应符合GB/T229的规定
D.4.3试样的制冷 试样进行冲击试验时,应制冷至规定温度,保温时间不少于5min. D.5弯曲试样和试验方法 D.5.1弯曲试样 弯曲试样厚度为试件原始厚度,焊缝应位于试样中心部位,且去除焊缝余高
当试样表面需平整加 工时,试样厚度应尽量接近于试件厚度
试样的长度L为200mm,宽度w为38 mm, ,见图D.2 17
GB/T18442.7一2017 图D.2弯曲试样 D.5.2弯曲试验方法 弯曲试验方法应符合GB/T232和GB/T2653的规定
弯曲角度180",焊接接头弯曲试验的弯头 直径为4倍试件厚度,且焊缝应位于变形最大处
D.6试验记录 试验记录至少包括下列内容 试验过程中采集的原始数据; a b) 材料拉伸试验的完整应力-应变曲线; 材料力学性能试验报告
c D.7资料保存 试件预拉伸及试验应至少保存下列资料备查 试验完成后的试样; a 试件材料的原始质量证明书 b c D.6中规定的试验记录和报告文件
18
GB;/T18442.7一2017 附录! 规范性附录) 应变强化处理 E.1应变强化处理 E.1.1基本要求 E.1.1.1应变强化场地应有可靠的安全防护设施,并经单位技术负责人和安全部门认可
应变强化过 程中,试验现场不得进行与试验无关的工作,无关人员不得在试验现场停留
E.1.1.2内容器应满足本部分和设计文件的要求
E 1.1.3与内容器焊接的零部件应在强化之前焊接
E.1.1.4应变强化实施前,焊缝应按7.5的要求经无损检测合格
E.1.1.5应变强化用水中氯离子含量不超过25mg/I
E.1.1.6内容器顶部(最高处)应设置排气接管,充液口位于内容器的底部
应变强化时,支座的设置 应不影响内容器的变形
将水加满容器后,至少等待15min以让溶解在水中的气体充分排尽
E.1.1.7应变强化过程中应保持内容器外表面的干燥,强化完成后应将水排净吹干
E.1.1.8特种设备监督检验机构应对应变强化过程进行见证和检验,并在应变强化报告中签字确认
E.1.2检测器具及控制系统 压力表精度应不低于1.
级,压力表数量应不少于2个,压力表的量程应为强化压力的 E.1.2.1 1.5倍~3.0倍
压力表应经校验合格并在检定有效期内
E.1.2.2内容器各拘束段可能产生最大变形的截面,均应采用经过标定的位移传感器测量周长
采用 的附加测量的钢尺,其最小刻度至少达到1mm,且应校验合格
E.1.2.3应变强化自动控制系统除应满足强化工艺要求外,还应满足如下要求: 能自动测量截面的周长变化,精度应不低于0.2mm; aa b 能按设定的时间间隔记录压力和位移的数据,并形成压力-时间与位移-时间的关系曲线 能自动控制应变强化时压力的变化,并维持所设定的压力; c 能按设定的压力停止点进行保压; e 应变强化处理结束时,能计算最大变形截面的变形量
E.1.3应变强化压力 应变强化压力应符合6.7的规定
E.1.4强化处理过程 E.14.1应变强化时应缓慢升压,最大升压速度不应超过0.5MPa/min
当压力升至设计压力时,经表 面检查合格后方可继续升压,升压速度不应超过0.1MPa/min
E.1.4.2当压力升到强化压力后应进行保压,保压过程中每隔不超过5min重复测量每个可能产生最 大变形的截面的周长,并计算该截面的周长变化率
周向变化率按下式进行计算 周向变化率=(实测周长一初始周长/初始周长
E.1.4.3同时满足下列两个条件时,可以终止保压,开始降压 19
GB/T18442.7一2017 保压时间不小于1h; a b)最后30min内的最大周长变化率不超过0.1%/h 注1:对于直径不超过2000mm的内容器,如果最后15min内满足最大周长应变率不超过0.1%/h的要求,则内容 器的强化时间可缩短至不小于30 min 注2:为了减少保压时间,压力达到强化压力后开始保压的最初0.5h内,可将强化压力提高5%,且不得超过1.6pe
E.1.4.4当压力下降到耐压试验压力时,保压时间应不少于30min,并按7.5,2的要求进行检查
E.1.4.5卸压结束后应计算强化处理后筒体最大变形截面的周长变化率
E.2应变强化处理记录 E.2.1应变强化过程至少应记录以下内容 升压过程的压力和时间; a 强化实施前、强化实施过程中和强化实施后的周长(或变化量)测量值 b 筒体变形最大截面的周长变化率; c d 任何影响内容器使用功能的形状、尺寸的显著变化; 设计文件规定的其他要求
e E.2.2当需进行二次强化时,还应记录二次强化的原因和相关数据 20
固定式真空绝热深冷压力容器第7部分:内容器应变强化技术规定GB/T18442.7-2017
固定式真空绝热深冷压力容器是一种用于储存和运输高压气体、液态气体和低温液体的设备。其中,内容器是其核心组成部分之一。
为了提高内容器的承载能力和抗压性能,在实际生产中,通常采用应变强化技术来加强其结构。
根据GB/T18442.7-2017《固定式真空绝热深冷压力容器 第7部分:内容器应变强化技术规定》,内容器应变强化分为局部应变强化和整体应变强化两种类型。
其中,局部应变强化是指在内容器的受力集中区域设置加强筋、加强圈等部件,以承受更大的压力和冲击载荷;而整体应变强化则是指通过改变内容器整体结构形式、增加材料厚度等方式来提高其整体承载能力。
除此之外,GB/T18442.7-2017还对内容器应变强化所需的试验方法、试验标准、检测要求等方面进行了详细规定,以确保内容器的安全性、可靠性和稳定性。
总之,固定式真空绝热深冷压力容器中的内容器应变强化技术规定是保障设备正常运行和人身安全的重要措施,在设计、制造和使用过程中必须严格遵守。