GB/T37428-2019
电弧炉热平衡测试与计算方法
Methodsofdeterminationandcalculationofthermalbalanceinelectricarcfurnace
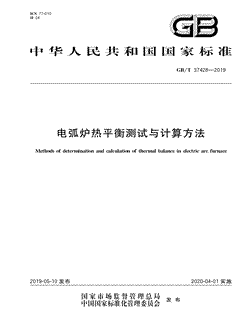
- 中国标准分类号(CCS)H04
- 国际标准分类号(ICS)77
- 实施日期2020-04-01
- 文件格式PDF
- 文本页数28页
- 文件大小1.49M
以图片形式预览电弧炉热平衡测试与计算方法
电弧炉热平衡测试与计算方法
国家标准 GB/T37428一2019 电弧炉热平衡测试与计算方法 Methosofdeterminationandcalculationofthermalbalanceinectricarcfurnace 2019-05-10发布 2020-04-01实施 国家市场监督管理总局 发布 国家标准化管理委员会国家标准
GB/37428一2019 前 言 本标准按照GB/T1.1一2009给出的规则起草
请注意本文件的某些内容可能涉及专利
本文件的发布机构不承担识别这些专利的责任
本标准由钢铁工业协会提出
本标准由全国钢标准化技术委员会(SAC/TC183)归口
本标准起草单位:北京科技大学、冶金工业信息标准研究院、光正能源有限公司、营口理工学院
本标准主要起草人:朱荣,董凯、彭煜华、王姜维、仇金辉、魏光升、马彦珍,丛伟、赵晶晶、李建军、 周东、吴学涛、田博涵
GB/T37428一2019 引 言 本文件的发布机构提请注意,声明符合本文件时,可能涉及第4章4.4.2.6.1与“一种电弧炉炼钢在 线测量钢液温度的测温系统及测温方法”(专利号ZL201510958681.7)相关的专利的使用
本文件的发布机构对于该专利的真实性、有效性和范围无任何立场
该专利持有人已向本文件的发布机构保证,他愿意同任何申请人在合理且无歧视的条款和条件下, 就专利授权许可进行谈判
该专利持有人的声明已在本文件的发布机构备案
相关信息可以通过以下 方式获得 专利持有人姓名:北京科技大学 地址:北京市海淀区学院路30号北京科技大学 请注意除上述专利外,本文件的某些内容仍可能涉及专利
本文件的发布机构不承担识别这些专 利的责任
GB/37428一2019 电弧炉热平衡测试与计算方法 范围 本标准规定了电弧炉热平衡测试的术语和定义、热平衡测试、物料平衡和热平衡计算方法
本标准适用于钢铁行业30t以上三相电弧炉热平衡测试与计算,直流电弧炉、其他行业的电弧炉 也可参照使用
规范性引用文件 下列文件对于本文件的应用是必不可少的
凡是注日期的引用文件,仅注日期的版本适用于本文 件
凡是不注日期的引用文件,其最新版本(包括所有的修改单)适用于本文件
GB/T34476转炉热平衡测试与计算方法 GB/T50439炼钢工程设计规范 术语和定义 GB/T34476、GB/T50439界定的以及下列术语和定义适用于本文件
3.1 冶炼周期taptotaptime 电弧炉从上炉出钢完成到本炉出钢完毕为止的时间
3.2 非接触测温non-contacttemperaturemeasurement 利用电弧炉炉壁喷枪喉口作为红外测温装置的测量窗口,并利用电弧炉炉壁喷枪喷吹测温气体产 生的超音速气体射流,排开炉膛内的含烟炉气,穿透钢液表面的泡沫渣层,在钢液和传感器之间建立起 稳定的钢液温度特征信号传输通道,实现电弧炉炼钢过程炉内钢液温度的连续或间断在线测量
热平衡测试 4.1热平衡测试基准 4.1.1基准温度 以炉体周围1m处的温度为基准温度
4.1.2热平衡测试范围 涵盖从加人原料到产出初炼钢水的全部设施包括废钢预热装置,电弧炉本体以及姻气余热回收装 置等
4.1.3测试工况和频次 测试在正常生产工况条件下进行,连续测试3次,每次测试一个冶炼周期
GB/T37428一2019 4.2测试准备 4.2.1设备状况 掌握电弧炉工艺及运行状况、基本情况,包括变压器、炉容量、炉型等;了解生产、检修状况,具体内 容详见附录A、附录B. 4.2.2制定测试方案 根据测试要求制定测试方案,并选择能够代表电弧炉实际生产情况的测试部位和测试点
4.2.3组织测试人员 根据测试方案组织测试人员
测试工作由专业技术人员指挥,按工作需要对测试人员进行分工,并 根据情况进行必要的技术培训与安全教育
4.2.4测试仪器、仪表准备 根据测试要求准备所需测试仪器、仪表
4.2.4.1 对现场已有仪表及各种便携的测量仪器进行校正,满足测试要求
4.2.4.2 工厂无计量装置时,在测试 前应安装符合测试要求的计量装置
4.2.4.3要求测试人员掌握各种仪器、仪表的使用方法和测量技巧,保证测量准确性
4.2.5预备性测试 正式测试之前对其中的几项或全部项目进行必要的预备性测试,验证测试手段的可靠性,检验测试 方案的安全性
4.3测试步骤 按测试内容进行测试与记录
采用以测量为主,控制中心记录数据为参考的方法,对所测数据进行 分析整理,并按本标准的计算方法进行计算
对测试结果进行分析并提供测试报告
创造必要的测试 条件,包括炉口测试平台,烟气取样口、电力接头的准备等
如现场无标准中规定的测试条件,亦可采用 现场能够满足测试要求的仪器装置进行测试
4.4测试内容、部位与方法 4.4.1主要测试内容 主要测试内容参见附录C
4.4.2测试部位与方法 4.4.2.1环境状况 用温度计测量炉体1m处温度
用气压计测量车间大气压
用干湿球温度计测量相对湿度,再换 算成绝对湿度
4.4.2.2耗电量的测量 电弧炉变压器一次侧三相累积电度表读取
GB/37428一2019 4.4.2.3辅助燃料用量的测量 现场测量
用炉前所安装的相应仪表读取辅助燃料(气体、液体燃料及固体燃料)的用量,并根据燃 料在炉前的压力、温度换算为标准状况下的值
4.4.2.4气体用量的测量 管道输送气体,由炉前安装的体积流量计读取气体流量数据;瓶装气体,在人炉管道上测量气体流 量数据
4.4.2.5质量的测量 对全部人炉料(包括废钢,生铁、铁水、矿石造渣剂、氧化剂、还原剂、补炉料等)及钢液(合格钢坯或 钢锭、铸余),炉渣,视现场条件,可用电子秤、磅秤等进行称量
进人炉渣中的炉衬量可视为炉衬被蚀 量;炉衬被蚀量可采用下线炉壳估算,或通过激光测厚仪进行测量,烟气含尘量采用按炉计量或采用高 温测尘仪测量
4.4.2.6温度的测量 4.4.2.6.1钢液温度的测量 钢液温度可采用快速热电偶如钨徕热电偶等)或非接触测温方法,在全熔、氧化期末和出钢前进行 测量
4.4.2.6.2炉渣温度的测量 在氧化期末和出钢前进行测量,可利用红外测温仪,双铂姥热电偶测量炉渣温度
在测量时,保证 热电偶插人渣层深度
用快速热电偶测定钢液温度,同时以定氧探头测定钢液与炉渣的温差,以其差值与快速热电偶测得 值之和可作为炉渣温度
4,4.2.6.3炉气温度的测量 炉气谢度采用抽气热电偶.双怕姥热电侧在第四孔或废斜预热中段进行调趾
应提前将热电偶装 人测试的指定位置并保证炉气测试位置与废钢温度测试位置一致
4.4.2.6.4炉尘温度的测量 取含尘量测定处炉气温度
4.4.2.6.5冷却水温度测量 采用水银温度计或酒精温度计,在进出口处分别测量水的温度
44.2.6.6入炉固体物料温度测量 人炉固体物料温度低时可采用半导体温度计、红外测量仪等测量,预热温度高时用热电偶、红外测 量仪测量
用半导体温度计、热电偶测量人炉炉料温度时,用设备依次测量多批次炉料温度,去掉第 次测量值,取其余测量值的平均值作为测量值
4.4.2.6.7入炉铁水温度测量 采用双铂姥快速热电偶测量或根据现场条件测量
GB/T37428一2019 4.4.2.6.8炉体表面温度及热流的测量 采用合适温度区间的红外测温仪或表面温度计测量,或采用热流计直接测试热流
测试过程中每 0.5m'炉体表面积取一个温度点,每3 min5min测量一次
4.4.2.6.9辐射温度的测量 开启炉盖及炉门时,炉盖、炉膛、炉门、电极、第四孔等的辐射温度,可采用光学高温计、红外测温仪 等设备进行连续测量
有热辐射计时,由于热辐射计可直接测量辐射热值,则上述温度值可不予测量
4.4.2.6.10余热回收量蒸汽量温度的测量 测量余热锅炉人口、出口烟气温度,烟气量以及蒸汽出口温度、压力、蒸汽量
4.4.2.7 面积的测量 炉体表面积参考图纸用量具进行测量 开启炉盖及炉门时,炉盖、炉膛、炉门电极、第四孔等的辐射面积,根据图纸计算,并按实测和观紫 进行修正
4.4.2.8冷却水流量的测量 宜安装流量测量装置进行测试,或用容器(秒表配合)测试各冷却部件的水流量但应保持测试中的 水压稳定
4.4.2.9辑射热的测量 采用热辐射计直接测试,没有热辐射计则按测出辐射温度后,根据辐射热公式进行计算
4.5化学分析 4.5.1入炉料的化学分析 对全部人炉料进行化学分析,测试或估算废钢氧化量及杂质含量
4.5.2钢液的全分析 包括全熔、氧化期末、出钢前钢样进行分析
终点碳的测量可以采用人工或炉门机器人插人钢液定 碳装置进行测量;钢液的过程碳成分,也可通过炉气分析,通过数据处理进行估算;出钢过程中用定氧探 头测定钢液中碳含量、氧含量
4.5.3炉渣的全分析 包括全熔、氧化期末、出钢前渣样进行分析
4.5.4炉气的分析 送电后10min开始用取样器取第一个炉气样,然后每间隔5min取一次样,炉气取样位置应无空 气吸人
应用气体分析仪或气相色谱仪等方法进行气体成分分析
以露点仪或高温测尘仪测定炉口炉 气的含水量;或采用炉气成分在线分析方法,取样探头从电弧炉第四孔或者废钢预热中段采集炉气,经 降温、除水和过滤粉尘,利用气体分析仪对炉气进行在线分析
GB/37428一2019 4.5.5炉尘成分分析 炉尘成分由含尘量测试处取样分析,或通过除尘设备计量并取样进行化学分析
物料平衡和热平衡计算方法 5.1物料平衡计算方法 5.1.1收入物料质量的计算 5.1.1.1收人物料质量总和按式(1)计算: 习G=G十G十G+G十G十G
十G十G,十G,十G十G十G+G(1 式中 习G 收人物料质量总和,单位为千克每吨(kg/t); 铁水质量,单位为干克每吨(kg/D) G G -生铁质量,单位为千克每吨(kg/t); G 废钢质量,单位为千克每吨(kg/); 石灰/白云石质量,单位为千克每吨(kg/t); G 镁砂质量,单位为千克每吨(kg/t); 铁矿石质量,单位为千克每吨(kg/t) G6 萤石质量,单位为千克每吨(kg/t); G 人炉气体质量,单位为千克每吨(ke/D G G 电极消耗质量,单位为千克每吨(kg/t); G 燃料消耗量,单位为千克每吨(kg/t); 碳粉质量,单位为千克每吨(kg/t); Gn 炉衬侵蚀质量,单位为千克每吨(kg/t): G1 混风量,单位为千克每吨(kg/t)
G1s 5.1.1.2炉衬侵蚀质量G;用钙镁平衡法按式(2)计算 =G'w十Gwe Gw G;w Gw Gw G 式中: -炉渣的质量,单位为千克每吨(kg/t); G G 炉尘的质量,单位为千克每吨(kg/t) 炉渣中任意组成物的质量分数,% w 炉尘中任意组成物的质量分数,%; 7" 石灰/白云石中任意组成物的质量分数,%; 7 7 -镁砂中任意组成物的质量分数,%; 铁矿石中任意组成物的质量分数,% w6 萤石中任意组成物的质量分数,%
w 5.1.1.3混风量G可由除尘设备抽气泵的工作参数以及水冷滑套的开度来计算电弧炉的混风量
或 条件允许时,采用炉气分析和N-Ar示踪平衡的方法计算电弧炉的混风量
5.1.2支出物料质量的计算 5.1.2.1支出总和习G')计算按式(3)计算
GB/T37428一2019 .(3 习G'=G十G十G'+G'十G'十G十4AG 式中 出炉钢液质量,单位为千克每吨(kg/t); G 出炉炉渣质量,单位为千克每吨(kg/t); G Ge 出炉炉尘质量,单位为千克每吨(kg/t); Ge -物料水分生成的水蒸气的质量,单位为千克每吨(kg/t) G 出炉炉气质量,单位为千克每吨(kg/t); 燃料带人及生成的水蒸气质量,单位为千克每吨(kg/t). G" 物料各项收人总和与已测各项支出总和的差值,单位为千克每吨(kg/t)
G 5.1.2.2物料各项收人总和与已测各项支出总和之差即为差值AG,按式(4)计算 AG=G一(G'十G'十G'十G'十G十G, ×100 差值包括未测出的支出及误差
物料平衡允许相对误差值为士5%以内,即 5.1.2.3物料水分生成的水蒸气质量G'按式(5)计算 G'=G"十G"十G,"十G" 5 式中 G" 人炉废钢的含水质量,单位为千克每吨(kg/); C" 白云石/石灰的含水质量,单位为千克每吨(kg/t); G" 铁矿石的含水质量,单位为千克每吨(kg/); G" 萤石的含水质量,单位为千克每吨(kg/t)
出炉炉气质量c按式(o计算 5.1.2.4 G" 28pco 十44f;十32f十28g - X22.4 一 式中 -炉口干炉气体积,单位为立方米每吨(m/t). v? 28 CO的摩尔质量,单位为克每摩尔(g/mol); -炉口干炉气中cO的体积分数,%; Pco -cO的摩尔质量,单位为克每摩尔(g/mol); 44 炉口干炉气中co的体积分数,%; geo 32 O的摩尔质量,单位为克每摩尔(g/mol); 炉口干炉气氧气的体积分数.%; o 28 -N的摩尔质量,单位为克每摩尔(g/mol); -炉口干氮气成分体积分数,%; PN 22.4 -标准状态下,炉气的摩尔体积,单位为升每摩尔(L/mol)
其中炉口干炉气体积V'由式(7)得出 187(Ge e+Ge生土nrGnm Pco十Pco02 式中 每吨钢中碳的氧化总质量,单位为千克每吨(kg/t); Gc 石灰与白云石分解出气体中的含碳质量,单位为千克每吨(kg/t); Gc分 燃料中C元素的烧损率,% 7RT GR 燃料中C元素质量,单位为千克每吨kg/t.
GB/37428一2019 其中G由式(8)计算得出: C=Gw十mcm十).G 式中: 钢铁料在冶炼中碳的氧化量,为最初炉料与最终钢水中碳的差值,单位为千克每吨(kg/t); Ge 电极烧损率,%; 7T 电极消耗量,单位为千克每吨(kg/) G1 电弧炉碳粉烧损率,%; pcce Ge 电弧炉中加人的碳粉,单位为千克每吨(kg/t). 5.1.2.5燃料带人及生成的水蒸气质量G按式(9)计算 G 9 GHoHGHow 式中 G -燃料中水的质量,单位为千克每吨(kg/t) 'HH 燃料中除水以外氢元素反应生成水的质量,单位为千克每吨(kg/t),按式(10)计算 G IHow l8 G 十" V 大 )一V'" "能+可驴a十早ns十 H0w 9s faM 22. (10 式中: V 含H元素气体燃料的人炉标准体积,单位为立方米每吨(m/t) -含H元素气体燃料中H
的体积分数,%; s CH,分子中氢原子的数量; 含H元素气体燃料中CH,的体积分数,%; m 含H元素气体燃料中H,S的体积分数,% 中心e 干炉气人炉体积,单位为立方米每吨(m'/t); 干炉气中H的体积分数,%; 会" 干炉气中CH的体积分数,%; 干炉气中H.s的体积分数,% 9'hs H.o的摩尔质量,单位为克每摩尔(g/mol)
18 5.1.3物料平衡记录表 将物料平衡各收,支项的计算结果记人表1中
表1物料平衡记录表 收人 支出 符号 项目 kg/t%(百分比 符号 项目 lkg/A%(百分比, 习G G G 出炉钢液质量 铁水质量 G 生铁质量 G 出炉炉渣质量 G 废钢质量 G 出炉炉尘质量 物料水分生成的水蒸气 G 石灰/白云石质量 F 质量 G 镁砂质量 G出炉炉气(干炉气)质量 燃料带人及生成的水蒸 铁矿石质量 气质量 萤石质量
GB/T37428一2019 表1续 收人 支出 符号 项目 kg/t%百分比 符号 项目 kg/t%百分比, G 人炉气体质量 G 电极消耗质量 燃料消耗质量 G G 碳粉质量 炉衬侵蚀质量 G G 混风量 差值 AG 100 100 习G 合计 合计 注1:百分率精确到小数点后一位
注2:热量值取4位有效数字
5.2热平衡计算 5.2.1热收入项 热量总收人习Q按式(11)计算 5.2.1.1 习Q=Q十Q十Q十Q+Q (11) 式中 人炉物料物理热量,单位为千焦每吨(kJ/t); Q 元素氧化放出的热量,单位为千焦每吨(k/t) Q 成渣反应放出的热量,单位为千焦每吨(J/t). 电热量,单位为千焦每吨(k/t); Q 燃料燃烧热量,单位为千焦每吨(k/t). 5.2.1.2人炉物料物理热量Q按式(12)计算
(12 Q=习G,(c.t,一ciet.十Q 式中 吨钢所加人的第i种除人炉铁水以外物料的质量,单位为千克每吨(kg/t); 第i种炉料在0C到间的平均比热容,单位为千焦每千克摄氏度[k/kg]; 第种物料的人炉温度,单位为摄氏度(C) 第i种炉料在0C至
间的平均比热容,单位为千焦每千克摄氏度[kJ/kgC] Ci 基准温度,单位为摄氏度(C); t
-吨钢人炉铁水所带人的物理热量,单位为千焦每吨(kJ/t)
Q 人炉铁水带人的物理热量Qr按式(13)计算: .t.十217.44十cr(t下一,] 13 Q=Gr[(cn GTtrCTet 式中 Gr 人炉铁水质量,单位为千克每吨(kg/); 人炉铁水0C到,之间的平均比热容,单位为千焦每千克摄氏度[kJ/(kg] CGT 人炉铁水熔点,单位为摄氏度(C); 人炉铁水在0C到
之间的平均比热容,单位为千焦每千克摄氏度[kk/kgC] CTe 人炉铁水在1,到t下之间的平均比热容,单位为千焦每千克摄氏度[k/(kgC] CYT 217.44 铁水的熔化潜热,单位为千焦每千克(k/lkg);
GB/37428一2019 -人炉铁水温度,单位为摄氏度(C)
5.2.1.3元素氧化放出的热量Q按式(14)计算: Q.=9199.52×"x(Gi十mrGim)十3276.llx一" 'x(G十aGir)十32169.0G 十7004.18Gn十24069.29Gp十9270.61×d.G十4775.39Go ,十7367.98G (14 F一Fe0 式中: C元素氧化成co的化学反应热,单位为千焦每千克(k/Akg); 9 199.52 C元素氧化为co的百分率,%; G 冶炼每吨钢C元素的氧化量,单位为千克每吨(kg/t); 燃料中C元素的烧损率,%; 7RT G财m 燃料中C元素的质量,单位为千克每吨(kg/t):; 32746,11 C元素氧化成CO,的化学反应热,单位为千焦每千克(k/kg); 32169.05 Si元素氧化的化学反应热,单位为千焦每千克(k/kg); Gs 冶炼每吨钢Si元素的氧化量,单位为千克每吨(kg/t); 7004.18 -Mn元素氧化的化学反应热单位为千焦每千克(kJ/kg); 冶炼每吨钢Mn元素的氧化量,单位为千克每吨(kg/t) GMm P元素氧化的化学反应热,单位为千焦每千克(kJ/kg); 24069.29 冶炼每吨钢P元素的氧化量,单位为千克每吨(kg/t) G 9 270.61 S元素氧化的化学反应热,单位为千焦每千克(kJ/kg): S元素氧化为SO的百分率,% G 冶炼每吨钢S元素的氧化量,单位为千克每吨(kg/t) 44 775.39 Fe元素氧化成FeO的化学反应热,单位为千焦每千克(J/kg) G 人炉炉料中Fe元素氧化成FeO的质量,单位为千克每吨(kg/t) rF-Fo 7367.98 Fe元素氧化成Fe.O的化学反应热,单位为千焦每千克(k/kg); 人炉炉料中Fe元素氧化成Fe.,O的质量,单位为千克每吨(kg/t)
Ge FeFeo 人炉物料中Fe元素氧化成Fe0和Fe.O的质量分别按式(15)和式(17)计算 56 15 Gpo GrFeFao 式中 -Fe的摩尔质量,单位为克每摩尔(g/mol); 56 72 -FeO的摩尔质量,单位为克每摩尔(g/mol); 人炉物料中氧化亚铁的生成量,单位为千克每吨(kg/t),按式(16)计算
Ge G =G +G'u-G.wx-G.us (l6 rFo" 2wx十 式中: 炉造中FdO含量,% w'x 炉尘中FeO含量,%; " Ze 废钢中Fe0含量,%; w'x 铁矿中石氧化亚铁含量,%
w 56X2 G G 17 FoFeo Fego 6Oo 式中: 56 -Fe的摩尔质量,单位为克每摩尔(g/mol); Fe元素反应生成Fe.O反应方程式中Fe元素的化学计量系数 160 -Fe.O的摩尔质量,单位为克每摩尔(g/mol);
GB/T37428一2019 人炉物料中Fe.O的生成量,单位为千克每吨(kg/t),按式(18)计算 Gs e2O Gneo=G'uw十G'w-Gw-G,w . 式中 炉渣中Fe.O含量,% w 炉尘中Fe.O含量,% w' -废钢中Fe.O含量,%; w 铁矿石中Fe,O含量,%
wy 5.2.1.4成渣反应放出的热量Q按式(19)计算 60 142 Q=2103.34G、十5093.19G 19 31×2 式中 2103.34 si元素氧化反应热,单位为千焦每千克(kJ/kg) 60 -SiO的摩尔质量,单位为克每摩尔(g/mol); 28 -Si的摩尔质量,单位为克每摩尔(g/mol); P元素的氧化反应热,单位为千焦每千克(kJ/kg); 5093.19 142 -PO.的摩尔质量,单位为克每摩尔(g/mol); P的摩尔质量,单位为克每摩尔(g/mol); 2 P元素反应生成P.O,反应方程式中P元素的化学计量系数
5.2.1.5电热量Q,按式(20)计算 20 598.24×w =3 Q= 式中 电热当量,单位为千焦每千瓦时[k/(kw
h]
3598.24 w 吨钢有功耗电量,单位为千瓦时每吨(kwh/),按式(21)计算 w W 21 W -总耗电量,单位为千瓦时(kw
h); G 每炉总钢液量,单位为吨(. 5.2.1.6燃料燃烧热量Q
按式(22)计算 =G,×g 22 Q 式中 吨钢燃料消耗量,单位为千克每吨(kg/t); G 燃料低位发热量,单位为千焦每千克(kJ/kg). q 5.2.2热支出项 热量总支出>Q'按式(23)计算 5.2.2.1 习Q'=Q'十Q'十Q十Q'十Q十Q十Q十Q
十Q,十Q十Q十AQ(23) 式中 -钢液带出的物理热量,单位为千焦每吨(k/t); Q Q' 炉渣带出的物理热量,单位为千焦每吨(k/) Q 炉尘带出的物理热量,单位为千焦每吨(kJ/t); Q 烟气中水燕气带出的热量,单位为千焦每吨(kJ/t); Q 中气带出的物理热量,单位为千焦每吨(k/D) 炉 物料分解反应吸收的热量,单位为千焦每吨(kJ/t) Q Q -冷却水带走的物理热量,单位为千焦每吨(k/t); Q -炉体表面散发的热量,单位为千焦每吨(k/t); 10
GB/37428一2019 Q -辐射损失的热量,单位为千焦每吨(k/t); Q -燃料化学不完全燃烧热量,单位为千焦每吨(k/t) Q 电损失热量,单位为千焦每吨(kJ/t) AQ 热量各项收人总和与已测各项支出总和的差值,单位为千焦每吨(kJ/t). 5.2.2.2热量各项收人总和与已测各项支出总合的差值按式(24)计算 Q=>Q-(Q'+Q'+Q'+Q'+Q'+Q'+Q:+Q:+Q'+Q+Q》(24) Q 热平衡允许相对误差规定为士5%,即 ×100<5
Q 5.2.2.3钢液带出的物理热量Q按式(25)计算 Q =G:[e一e.l十271.8十'('一h 25 式中 出炉钢液在0C至t
间的平均比热容,单位为千焦每千克摄氏度[kJ/kgC] e' -钢种熔点,单位为摄氏度(C); 出炉钢液在0C至,
间的平均比热容,单位为千焦每千克摄氏度[kI/(kg
C]; C
271.8 钢的熔化潜热,单位为千焦每千克(kJ/kg); c -出炉钢液在
至间的平均比热容,单位为千焦每千克摄氏度[k/kg]; -出钢温度单位为摄氏度(C)
5.2.2.4炉渣带出的物理热量Q按式(26)计算 26 Q=G'(e''一c'k./.十209.08) 式中 炉渣在0C至t'间的平均比热容,单位为千焦每千克摄氏度[CkJ/kgc] cc 出炉炉渣的温度,单位为摄氏度(C); tt" e么 -炉渣在0至
间的平均比热容,单位为千焦每千克摄氏度[k/kg
]
209.08 -渣的熔化潜热,单位为千焦每千克(k/kg). 炉尘带出的物理热量Q按式(27)计算 5.2.2.5 27 Q'=G'(e't一c'.t
十209.08) 式中 炉尘在0C至t间的平均比热容,单位为千焦每千克摄氏度[kJ/(kg
C] ce t" 出炉炉尘的温度,单位为摄氏度(C); c' -炉尘在0至
间的平均比热容,单位为千焦每千克摄氏度[k/(kg
]; 209.08 炉尘的熔化潜热,单位为千焦每千克k/kg)
5.2.2.6烟气中水蒸气带出的热量Q'按式(28)计算 Q=(G'+G)[e.(100一t.)十2253.88十1.24(c,t'一15.05) 28 式中 水在人
至100C平均比热容,单位为千焦每千克摄民度(k/(kg" ,C)); -水蒸气的汽化潜热,单位为千焦每千克(kJ/kg); 2 253.88 1.214 -水燕气的密度,单位为千克每立方米(kg/m'); -水蒸气在0C至'间的平均比热容,单位为千焦每千克摄氏度[k/(kgC]; 炉口处炉气的温度,单位为摄氏度(C)
5.2.2.7炉气带出的物理热量Q按式(29)计算 29 Q=G'(e''一c. 式中: 炉气在0C至'间的平均比热容,单位为千焦每千克摄氏度[kJ/(kgC]; C5 -炉口处炉气的温度,单位为摄氏度(C) -炉气在0C至/.
间的平均比热容,单位为千焦每千克摄氏度[kI/(kgC)]
1
GB/T37428一2019 5.2.2.8物料分解反应吸收的热量Q按式(30)计算 Q
=5151.73Go十4072.88Gc-cao十2304.06Gco-Mseo 式中 5151.73 -物料分解成FeO所需要的化学反应热,单位为千焦每千克(k/kg); 072.88 石灰和白云石中CacO分解成cO,所需要的化学反应热,单位为千焦每千克(kJ/ 44 kg); 石灰和白云石中CacO生成co.的量,单位为千克每吨(kg/t); Gcogc.co 2304.06 白云石中MgCO分解成cO所需要的化学反应热,单位为千焦每千克(/kg); 白云石中MgCo生成二氧化碳的量,单位为千克每吨(kg/t) Ge rco2-Mgeco 5.2.2.9冷却水带走的物理热量Q按式(31)计算 (31 Q=习G,(caw/e一ci/iw 式中 G -第;个冷却部件使用冷却水的质量,单位为千克每吨(kg/t) -冷却水在0C至t间的平均比热容,单位为千焦每千克摄氏度[kJ/kgC] C2w 第i个冷却部位冷却水出水的温度,单位为摄氏度(); 'aw 冷却水在0C至4i间的平均比热容,单位为千焦每千克摄氏度[kJ/(kg] C1w 第i个冷却部位冷却水进水的温度,单位为摄氏度(C 1w 5.2.2.10炉体表面散发的热量Q'按式(32)计算 T习q.A Q
- 60G 式中 电弧炉冶炼周期,单位为分(min). -第i部分炉体表面平均面积热流量,单位为千焦每平方米小时[k/mh],如不能直接 g 测量,可按式(33)计算 -第部分炉体表面散热面积,单位为平方米(m'); D ,23土上 3土上 =20.4le 33 +a.( 一t
q 100 100 式中 辐射换热系数,单位为千焦每平方米小时[k/(m 20.41 h)门; 第i部分炉体表面黑度; -第部分炉体表面平均温度,单位为摄氏度(C); t -对流给热系数,单位为千焦每平方米小时[kJ/mh)]
aa 无风时,对流给热系数按式(34)计算 =A(一,.)t 34 a 式中 系数,散热面向上时A=11.7,向下时A=6.3,垂直时A=9.2 当风速w<5m/s时,对流给热系数按式(35)计算 35 e=22.2+15.1w 式中 W -风速,单位为米每秒(m/s). 当风速w>5m/s时,对流给热系数按式(36)计算 =27.1ww7" (36 a 5.2.2.11 辐射损失的热量Q按式(37)计算 真[23十-(2r3十 Q=习20.41 37 , 100 100 G 12
GB/37428一2019 式中: A" 部位辐射面积,单位为平方米(m); 部位辐射角度系数; 声 部位黑度; 部位辐射时间,单位为分(min); T 部位的辐射温度,单位摄氏度(C). ti 5.2.2.12燃料化学不完全燃烧热量Q按式(38)计算: 22.4 (38 Q=V.(126,.35×f十 1o7.9x另+58.:7X只w十)-1a.石x HG义" 12 式中: 126.35 -1mCO完全燃烧时放出的热量,单位为千焦每立方米(k/m'); 干炉气中co的体积分数,%; 07.9 lmH完全燃烧时放出的热量,单位为千焦每立方米(kJ/m') 干炉气中H
的体积分数,%; 中 358.57 lmCH完全燃烧时放出的热量,单位为千焦每立方米(k/m'); 干炉气中CH的体积分数,%; m 12 C的摩尔质量,单位为克每摩尔(g/mol); Ge -碳元素的氧化量,单位为千克每吨(kg/t); C元素氧化成co的百分率,%
5.2.2.13电损失热量Q按式(39)式(44)计算: 3598.24 Q=3R
39 1000 了-下×1000/5cose 40 l2 W 41 W cos一 42 V/WQW 43 Qw=AQw×m u2r 44 4 式中 平均电流,单位为安(A); 相电阻,单位为欧(Q),按式(45)计算, 全炉总通电时间,单位为小时(h) 全炉钢液量,单位为吨(t); 598.24 电热当量,单位为千焦每千瓦时[kJ/(kwh)] 3 平均功率,单位为千瓦(kW); -功率因数 cose 二次侧平均电压,单位为伏(V); -全炉总电耗(有功),单位为千瓦时(kw
h); 全炉无功消耗,单位为千瓦时(kwh); Q -无功电度表读数,单位为千伏安每小时(kVA/h); AQw 无功电度表倍率; 二次各级电压,单位为伏(V). 各级电压使用时间,单位为小时(h) 13
GB/T37428一2019 R =R十R,-Ri (45 式中 每相短网平均电阻,单位为欧(Q); 变压器每相平均电阻,单位为欧(Q); R R -炉盖下电极电阻,单位为欧(Q)
短网及变压器的相电阻按式(46)计算 R=R十Ra一R 46 式中 短网每相电阻,单位为欧Q)3 R
电极每相电阻,单位为欧(Q) 当考虑短网和变压器损失时,电损失热量Q按式(47)计算 3598.24 -3308.21w十3了对 Q (47 000 式中: Aw 短网和变压器损失,单位为千瓦时每吨[kwh/]; 3598.24 3'R" 把持器以下至炉盖间电极电阻损失,单位为千焦每吨(kJ/t); 1000 把持器至炉盖间电极每相电阻,单位为欧(Q) R" 5.2.3热平衡表 由热平衡各收,支项热量的计算结果列于表2
表2热平衡表 支出 收人 %(百分比 %(百分比、 符号 J/t 符号 kJ/t 项目 项目 Q 人炉炉料物理热量 Q 钢液带出的物理热量 Q 人炉铁水带人的物理热量 Q 炉渣带出的物理热量 Q 元素氧化放出的热量 Q 炉尘带出的物理热量 成渣反应放出的热量 2 烟气中水蒸气带出的热量 Q Q 炉气带出的物理热量 电热量 Q Q" 燃料燃烧热量 物料分解反应吸收的热量 Q 冷却水带走的物理热量 炉体表面散发的热量 辐射损失的热量 Q 燃料化学不完全燃烧热量 Qm 电损失热量 AQ 差值 合计 100 习Q 合计 100 注1;百分率精确到小数点后一位 注2热量值取4位有效数字 14
GB/37428一2019 5.3回收项 余热锅炉的有效利用热量按式(48)计算: (h,一h
48 Q= 3600 式中 余热锅炉的有效利用热量,单位为千焦每秒(kJ/s); Q. 余热锅炉烟气人口熔,单位为千焦每小时(kJ/h); n 余热锅炉烟气出口熔,单位为千焦每小时(kJ/h); n 锅炉热效率,%
当余热锅炉人口姻气条件稳定时,对饱和蒸汽锅炉,锅炉蒸发量按式(49)计算 r p 49 D=Q (i一i (i一i 100 100 式中: D 锅炉蒸发量,单位为千克每小时(kg/h); 饱和蒸汽熔,单位为千焦每千克(k/kg) i -饱和水熔,单位为千焦每千克(k/kg); ie 给水烙,单位为千焦每千克(k/kg); i 汽化潜热,单位为千焦每千克(k/kg); 燕汽湿度,%; 锅炉排污率,%
P 5.4热效率 热效率按式(50)计算: Q'+Q'-Q十60rQ ×100% 7R一 Q Q 式中: 电弧炉热效率,%
7R 5.5主要经济技术指标记录表 主要经济技术指标记人表3
表3主要技术经济指标记录表 指标 单位 数值 吨钢电耗(合格锭 kwh/t 吨钢电极消耗 kg/ 吨钢氧耗 m'/t 吨钢铁水消耗 kg/t 吨钢废钢消桃 kg/t 吨钢燃料消耗 kN/ 吨俐蒸汽回收量 kg/t 15
GB/T37428一2019 5.6热平衡测试报告内容 热平衡测试报告应至少包括以下内容 a 前言; 主要设备概况及生产状况 c 主要测定数据; d 物料平衡表; 热平衡表; e f 热效率; 分析与改进建议; 8 h)测定单位、测试人员,负责人、报告人,审核人(签字)
16
GB/37428一2019 附 录 A 资料性附录 设备及电弧炉概况 设备及电弧炉概况记人表A.1
表A.1设备概况 内容或数值 项目 单位 车间名 炉号 炉型 炉容 熔池深度 炉龄 -次侧电压 电极直径 mm 装料方式 lkVA 变压器容量 二次侧电压 燃料种类 余热利用 17
GB/T37428一2019 录 附 B 资料性附录) 测试前一年生产状况 测试前一年(不足一年按实际炉次计算)生产概况记人表B,1
表B.1测试前一年生产概况 项目 单位 内容或数值 钢种 炉数 时间范 供氧 min 辅助 min 平均 时间 故障 min 全炉 minm 钢铁料 kg/t 铁水 kg/t 平均 废钢铁 kg/t 单耗 其他 kg/t 氧气 m/t 炉渣量 kg/t % 吹损率 18
GB/37428一2019 录 附 C 资料性附录 主要测试项目 主要测试项目结果表记人表c.1
表c.1主要测试项目结果记录表 企业名称及电弧炉编号 熔炼钢种 测定单位和日期 项目 单位 内容 测量温度 吨钢耗量 kg/t 其他 kg/t % 废钢 Mn 不 废钢的化学成分 % C N A 人炉温度 吨钢耗量 kg/t 铁水 S 铁水平均化学成分 Mn 人炉温度 吨锻耗量 kg/t Si 不 生铁 生铁平均化学成分 Mn % 人炉温度 吨耗量 kg/" 直接还原饮 Si % 直接还原铁 Mn 平均化学成分 % 19
GB/T37428一2019 表c.1续 企业名称及电弧炉编号 熔炼钢种 测定单位和日期 项目 单位 内容 人炉温度 吨钢耗量 kg/" CaO % MgO 石灰 石灰平均化学成分 AlO. SiO. % CO 人炉温度 吨钢耗量 kg/ MgO 镁砂 CaO % SO. 镁砂平均化学成分 Al.O 人炉温度 吨钢耗量 kg/t 净铁矿石量 kg/t Fe % 铁矿石 FeO. SiO 铁矿石平均化学成分 MnO % Al.O MgO 人炉温度 吨钢耗量 kg/t 净萤石量 kg/t CaF 萤石 CaO 净萤石平均化学成分 Al,(O MgO 人炉温度 吨钢耗量 kg/" 净白云石量 kg/t MgO % 白云石 Ca(O 净白云石平均 SiO % A.O % 化学成分 CO. % 20
GB/37428一2019 表c.1续 企业名称及电弧炉编号 熔炼钢种 测定单位和日期 项目 单位 内容 人炉温度 吨钢消耗 kg/" CaO % 炉衬 MgO % 炉衬平均化学成分 SiO Al,(O 人炉温度 吨钢消耗 kg/t 氧化铁皮 氧化铁皮平均 FeO 化学成分 贝 Fe.O 人炉温度 吨钢耗量 kg/t Si Fe % 硅铁 Mn 硅铁平均化学成分 % A % 人炉温度 吨钢耗量 kg/t % Mn Fe % 猛铁 不 征铁的平均化学成分 % 人炉温度 吨钢耗量 kg/" 铝 Al 平均化学成分 % 人炉温度 吨耗量 kg/t CH % 天然气 天然气平均成分 CO H 21
GB/T37428一2019 表c.1续 企业名称及电弧炉编号 熔炼钢种 测定单位和日期 项目 单位 内容 天然气平均成分 天然气 % 人炉温度 吨钢耗量 kg/t 煤粉 % 煤粉平均化学成分 % 人炉温度 吨钢耗量 kg/t % 碳粉 不 碳粉平均成分 % 人炉温度 吨钢耗量 kg/" % % 石墨粉 石墨粉平均成分 % 人炉温度 吨钢耗量 kg/t 氧气 O % 氧气平均化学成分 % 人炉温度 吨钢耗量 kg/t 叙气 % 氯气平均化学成分 出钢温度 钢液量 kg/t 钢液 % 钢液平均化学成分 Mn % 22
GB/37428一2019 表c.1续 企业名称及电弧炉编号 熔炼钢种 测定单位和日期 项目 单位 内容 钢液 钢液平均化学成分 % 出渣温度 炉渣量 kg/t Ca(O SiO. 炉渣 MgO 炉渣平均化学成分 Mn(O P.O 不 炉尘温度 炉尘量 kg/t Fe(O % 炉尘 Fe.O. Cao 炉尘平均化学成分 SiO % 炉气温度 炉气量 kg/t C(g C(O 炉气 O 炉气平均化学成分 w % 冷却水 冷却水量 kg 水冷炉盖 进水温度 出水温度 冷却水量 kg 水冷氧枪 进水温度 出水温度 冷却水量 g 水冷炉壁 进水温度 出水温度 散热面积 m 炉盖 表面平均温度 表面平均面积热流量 k/m 表面散热 散热面积 m 上炉壳 表面平均温度 表面平均面积热流量 kJ/m'h) 23
GB/T37428一2019 表c.1续 企业名称及电弧炉编号 熔炼钢种 测定单位和日期 项目 单位 内容 散热面积 m 炉底 表面平均温度 表面平均面积热流量 k/m
表面散热 散热面积 m 康斯迪 表面平均温度 表面平均面积热流量 k/nm 辐射面积 m 炉腔 辐射表面温度 辐射热 k 辐射面积 m 电极 辐射表面温度 辐射热 kJ 辐射散热 辐射面积 mm O 炉门 辐射表面温度 牺射热 k 辐射面积 m 第四孔 辐射表面温度 牺射热 kJ 电耗 初始读数 终了读数 有功电度表 变化 kwh 有功消耗 无功消耗 kVar 初始读数 终了读数 无功电度表 变化 kW 有功消耗 无功消耗 kvar 24
GB/37428一2019 表c.1续 企业名称及电弧炉编号 熔炼钢种 测定单位和日期 项目 单位 内容 余热锅炉烟气人口温度 余热锅炉烟气出口温度 余热锅炉烟气量 kg/t 余热回收 燕汽出口温度 蒸汽出口压力 kPa 蒸汽量 kg/t 25
电弧炉热平衡测试与计算方法GB/T37428-2019
电弧炉是一种重要的冶金设备,在钢铁、有色金属等领域都有广泛应用。为了保证电弧炉的高效、稳定运行,需要进行热平衡测试,以确定炉内各部位温度分布、热流分布等参数。
1. 热平衡测试的基本原理
热平衡测试是指在电弧炉正常工作条件下,通过测量炉体及其零部件表面的温度值,并经过一系列计算处理,来确定电弧炉内部的热平衡状态。
电弧炉热平衡测试旨在确定以下参数:
- 炉前、炉后壁温度;
- 炉墙厚度;
- 炉墙材料的导热系数;
- 电极、电极下部和底板的温度;
- 炉内、外侧表面的辐射热流密度;
- 电弧功率、电极电流和电压等参数。
2. 热平衡测试的计算方法
根据GB/T37428-2019标准,电弧炉热平衡测试的计算方法可分为以下步骤:
- 确定炉内各测点的位置及编号;
- 对各测点进行测量,得到温度值;
- 通过热传导方程计算电弧炉壁的热流密度;
- 利用热平衡方程求解电弧功率和电极功率的大小;
- 计算电弧炉内各部位的热平衡状态,并绘制热平衡图。
3. GB/T37428-2019标准的要求
GB/T37428-2019标准明确了电弧炉热平衡测试的相关要求,包括:
- 测试时应保持电弧炉正常工作状态,实测数据应符合稳态条件;
- 测试需考虑环境因素对测试结果的影响,并在测试报告中进行说明;
- 测试结果应包括电弧功率、电极功率、电极下部温度、底板温度、炉内辐射热流密度等指标。
4. 总结
电弧炉热平衡测试是确保电弧炉高效、稳定运行的重要手段。通过GB/T37428-2019标准规定的计算方法和测试要求,可以对电弧炉内部的热平衡状态进行准确评估,从而提高电弧炉的生产效率和优化冶炼工艺提供科学依据。
总之,电弧炉热平衡测试是一项非常重要的工作,在钢铁、有色金属等领域都有广泛应用。通过本文的介绍,希望读者能够了解电弧炉热平衡测试的基本原理、计算方法和GB/T37428-2019标准的相关要求,从而更好地掌握该项技术。